As Amazon’s vice president of Global Workplace Health and Safety, I lead the organization of more than 10,000 safety professionals dedicated to keeping over 1 million employees safe, every day. Nothing is more important than ensuring our people’s safety because we know each and every person is someone’s mother, father, sibling, child, or best friend, and it’s why we’ve set an ambitious goal to become the benchmark of safety excellence across all industries in which we operate.
2024 was an impactful year: We focused on expanding and executing an effective strategy to improve safety across our global operations, and it led to meaningful, measurable progress. While I’m encouraged by our continued progress, we know there’s more work to do, and we’re committed to further improvement as we work toward our goal.
Today, I’m pleased to share our full-year 2024 data for our worldwide operations network that demonstrates consistent year-over-year improvement worldwide.
Here are some key updates from across our global operations:
- Our Recordable Incident Rate (RIR)—which includes any work-related injury that requires more than basic first-aid treatment—has improved 34% over the past five years and over 6% year over year (YoY).
- Our Lost Time Incident Rate (LTIR)—which includes any work-related injury that requires someone to take time away from work (the most serious injuries)—has improved 65% over the past five years and 13% YoY.
In the U.S., we report our operations data to the Occupational Safety and Health Administration (OSHA) under various industry codes that reflect the kind of work we do across our network. The majority of our data is reported under the General Warehousing and Storage and Courier and Express Delivery Services codes. As seen below, we continued making year-over-year progress across all categories, building on our meaningful progress over the past five years.
- In the U.S. General Warehousing and Storage industry:
- Our RIR improved 27% over the past five years and 5% YoY.
- Our LTIR improved 79% over the past five years and 9% YoY.
- In the U.S. Courier and Express Delivery Services industry:
- Our RIR improved 50% over the past five years and 16% YoY.
- Our LTIR improved 74% over the past five years and 25% YoY.
Evaluating our safety performance
The following graphs illustrate our progress year over year and how we stack up against industry averages calculated by The Bureau of Labor Statistics (BLS). The BLS calculates these averages using data from selected employers and releases them each November, so the most recent averages available are for 2023.
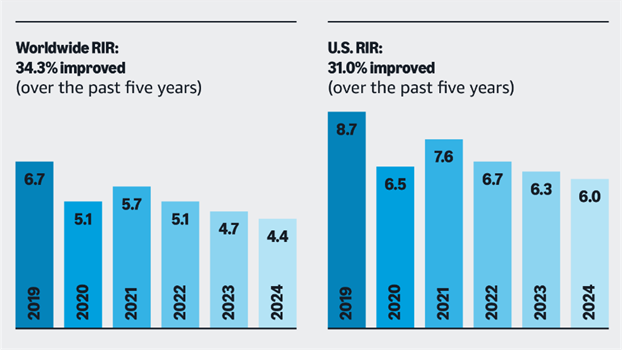
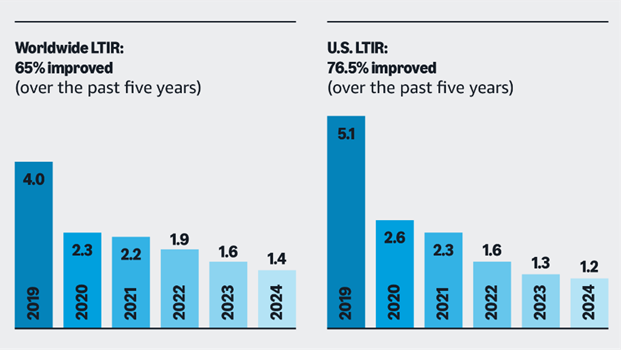
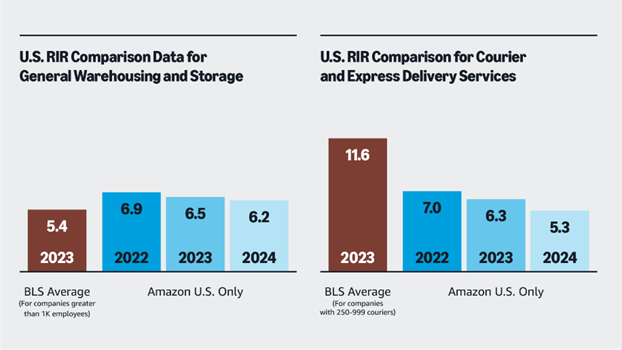
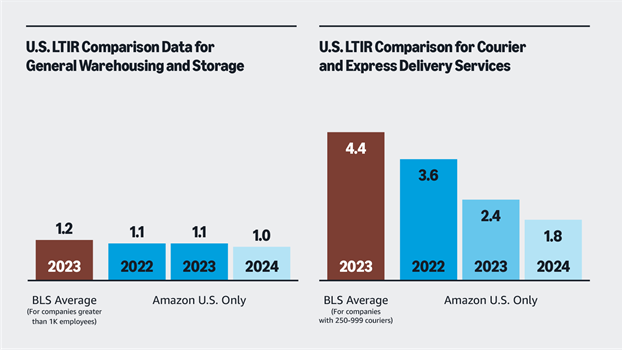
As the graphs illustrate, we’re continuing to make steady and meaningful progress. That said, we’ve never aspired to be average because when it comes to safety there is no such thing as “good enough.” We want to be the safest company in the industries in which we operate, so we’re consistently innovating and investing in safety measures. In 2025 alone, we’ve allocated hundreds of millions of dollars to invest in technologies, resources, training, and programs to further our safety efforts. You can read on to dive a bit deeper into our operations and progress.
Understanding our operations and workforce
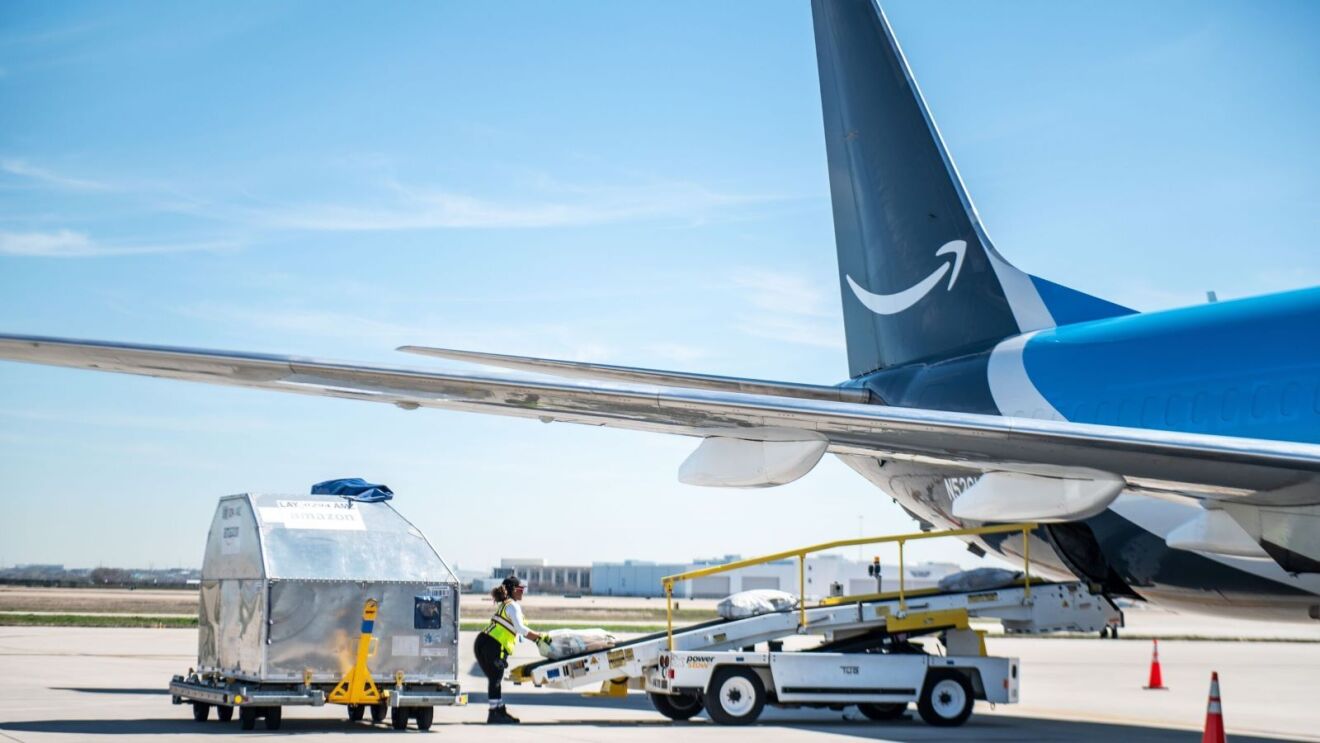
When looking at our data, it’s important to understand the basics about our operations and workforce. Globally, our operations network has more than doubled in size since 2019—to more than 1 million employees across more than 2,500 sites across the world. Alongside that growth, we’ve worked hard to further build and evolve our culture of safety.
We know that we can’t get safety right without our employees’ feedback. This past year, I visited our teams around the world—including Japan, Australia, UK, Germany, France, Italy, India, the UAE, and more—and saw firsthand how our dedication to fostering a dialogue on safety is making a positive impact. We’ve created several ways for employees to give us feedback on how to improve, but one tool I’m especially proud of is Dragonfly. Available on employees’ devices or at on-site kiosks, Dragonfly enables employees to provide suggestions from the palm of their hand and notifies their site managers who then take appropriate action as needed. In 2024, over 130,000 employees used Dragonfly to provide suggestions. Some recommendations include small changes like repositioning a package scanner so it isn’t accidentally knocked over, while others involve more complex safety measures like adding laser motion sensors to alert forklift drivers when people are nearby. Whether simple or sophisticated, these improvements make a big difference at scale in creating a safer, simpler employee experience.
We also invest heavily in offering competitive pay and benefits, which we know are important to helping our team lead healthy lives. Our regular full-time operations employees earn an average hourly base wage of more than $22 per hour and average compensation of more than $29 per hour when including the value of our wide range of elected benefits: from having health care starting day one, to mental health resources, to pre-paid college education, and on-the-job training. Also, our U.S. eligible hourly team members now receive Prime membership at no additional cost as long as they are a part of the Amazon team. If you want to learn more about our operations or the range of jobs available at Amazon, you can visit our website or register to take a tour of one of our facilities, which are open to the public.
Auditing and inspecting our sites
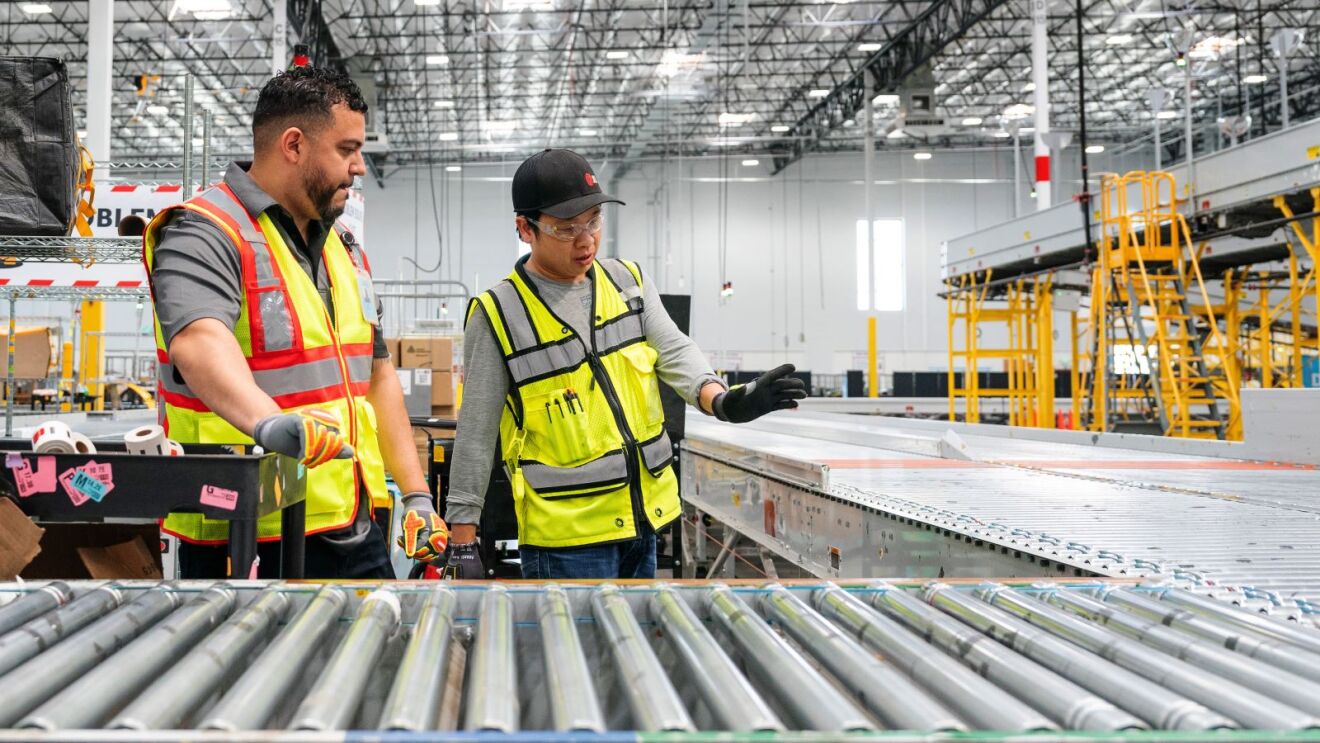
We consider both employee feedback and data when we’re identifying opportunities for improvement and developing proactive safety measures. This approach allows us to not only evaluate overall injury rates but also analyze the types and frequencies of injuries to help prevent them from happening in the first place. It’s why we rigorously audit and inspect our sites to make sure our resources and protocols are effectively helping us identify, eliminate, or reduce safety hazards. In 2024, we conducted 7.8 million inspections globally—a 24% increase from the 6.3 million conducted in 2023—and we audited 331 sites across Amazon.
These audits and inspections also help us determine how to address the various types of injuries. The most common injury in any workplace—across all industries—is what’s called a musculoskeletal disorder (MSD), more commonly known as a strain or sprain. Over the past five years, the rate of MSD recordable incident rates at Amazon has improved 32%, but they still make up about 57% of all recordable injuries at Amazon. To continue reducing MSD injuries, we’ve devoted considerable resources to improve ergonomic conditions as part of our ongoing investments in safety improvements.
Investing in safety improvements
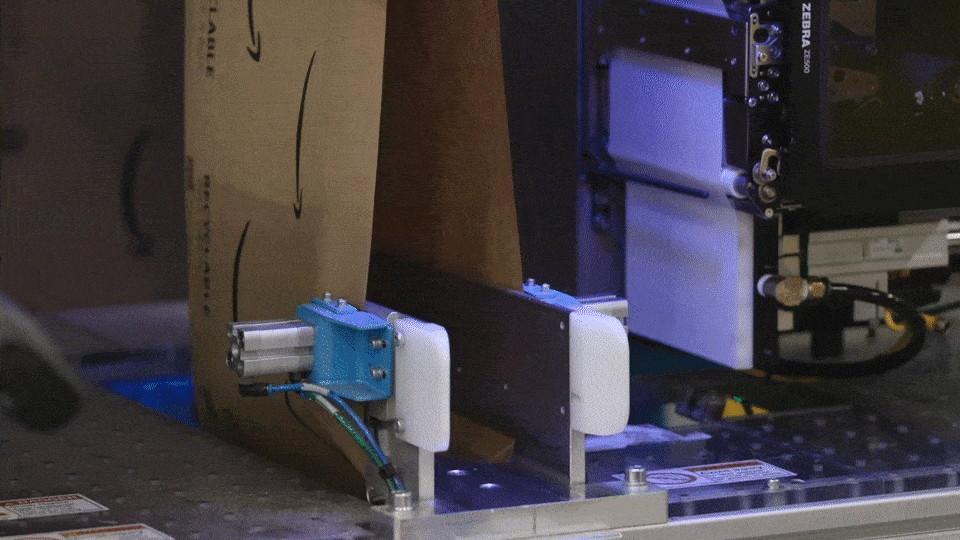
Since 2019, we’ve invested more than $2 billion in our safety efforts, including new technologies and programs to protect our employees. A key part of this investment is our focus on reducing MSD injuries. Across our operations network, we are retrofitting our sites with adjustable height workstations and carts, and implementing our proprietary, award-winning ErgoPick technology to ensure employees pick packages within their ergonomic power zone—the area between the shoulder and mid-thigh. We’ve also increased the use of robotics in our warehouses to handle repetitive tasks and heavy lifting that can lead to MSDs, supporting a safer workplace. Robot systems like Robin and Cardinal help sort, lift, and place packages. They handle repetitive and strenuous tasks so our employees can work more comfortably. Additionally, one of our newest robotics systems, Sequoia, transports inventory directly to employees’ workstation at an ergonomically friendly height, eliminating the need for them to reach above their heads or squat down. These are just a few examples of the innovations we’ve created to provide a safer work environment for our employees so they can focus on more engaging tasks.
In addition to investing in new technology, we also plan for things like extreme weather that can impact our employees’ and partners’ safety, and our policies and procedures for addressing the heat and cold are robust and often exceed industry standards. For example, Amazon branded vans come equipped with AC, which is above industry standards, and if it isn’t working, the vehicle is taken out of service immediately. We also prioritize understanding emerging safety trends to help create safer working environments. As an example, while we hope to never have to use it, we stocked naloxone, an over the counter opioid overdose reversal medication, in our U.S. and Canada fulfillment centers to proactively strengthen our emergency response procedures.
We’re also proud that last year, we received eight different safety awards from respected organizations including the National Safety Council, Verdantix, and the Network of Employers for Traffic Safety. These awards recognized safety innovations like our proprietary ErgoPick, our AI-enabled sensor technology that helps reduce risks when loading trailers, our cutting-edge employee training programs, and our world-class safety professionals.
Working safely with our operations partners
Within our operations network, we work with partners around the world to deliver packages to our customers safely and efficiently. For example, we work with small business owners called Delivery Service Partners (DSPs) and independent contractors called Amazon Flex delivery partners to deliver packages to customers’ doorsteps. We also work with independent, long-haul trucking companies to move products across our network. We’re committed to helping our partners keep their employees safe by offering them access to industry-leading safety technologies, resources, and training.
To help keep drivers and communities safe, we’re constantly designing and implementing new safety improvements to our branded vans used for last mile delivery. For example, all Amazon branded vans are equipped with camera-based technology that helps monitor safe driving behaviors. The system provides real-time feedback on key safety behaviors including speed control, maintaining focus, proper seat belt use, and adherence to road signs. If unsafe behaviors are detected, drivers receive coaching notifications during their delivery stop, and if the behaviors do not improve, the driver’s employer—the DSPs—are notified so they can further coach the driver. We’re also introducing live safety cues (audible and visual) for drivers that proactively inform them of low clearances bridges, railroad crossings, unpaved roads, and areas where they need to have additional awareness such as school zones. We’ve enhanced the Amazon Flex app for delivery partners using their own vehicles with safety-focused features. These include alerts for potential roadway hazards and the presence of pets at delivery locations, as well as a new chat feature that lets delivery partners notify customers when they’re approaching.
Last year, we also began rolling out our latest invention: Vision-Assisted Package Retrieval (VAPR) technology. VAPR reduces time drivers spend looking for packages in their van. Based on early tests, results yielded a 67% reduction in perceived physical effort, and we’re excited to continue this rollout.
For long-haul transportation, we've made investments in safety through our Relay technology, which carriers use to book and execute work for Amazon. This includes implementing stringent driver ID verification for every load to ensure we know exactly who is handling our shipments. We’ve also enhanced our safety guidance and trip planning features that provide drivers with route-specific weather forecasts, in-app alerts, and satellite imagery for safe navigation. We also improved our fleet of more than 50,000 branded trailers by adding flashing auxiliary lamps and reflective tape to ensure trailers are more visible to help drivers on the road maintain a safe distance.
Ultimately, we recognize that our scale demands exceptional road safety—a commitment recently acknowledged by the Fédération Internationale de l’Automobile’s (FIA) highest rating. It’s why we’re relentlessly creating and iterating new safety improvements for our partners to help keep them and the communities where they operate safe.
Looking ahead
2024 marked another year of meaningful progress, and I’m humbly proud of the team’s dedication to continuous improvement. Our goal to be the global benchmark of safety excellence is certainly ambitious, but I’m confident we’ll achieve it.
I’d like to extend a sincere THANK YOU to our employees and partners for their dedication to safety and feedback that helps us continually improve. Together, we’re making Amazon safer every day.
Trending news and stories
- Getting started with Alexa+: How to set up and personalize your experience
- 8 movies from Prime Video and Amazon MGM Studios coming soon in fall 2025
- How to watch ‘Superman,’ directed by James Gunn, on Prime Video
- Amazon now offers same-day perishable grocery delivery in over 1,000 cities and towns with plans to double that reach by year's end