A little more than 10 years ago, I graduated with a degree in finance from the University of the Pacific in Stockton, California. Like many new graduates, I was eager to enter the workforce, but I also wondered what life would look like for me after school.
My father had recently joined Amazon, working at a fulfillment center in the area. He encouraged me to join him as an Amazon employee after learning about a new site opening nearby. I initially started by picking and packing customer orders, and a decade later, I now help run a robotics fulfillment center in Tracy, California, which employs 1,500 people.
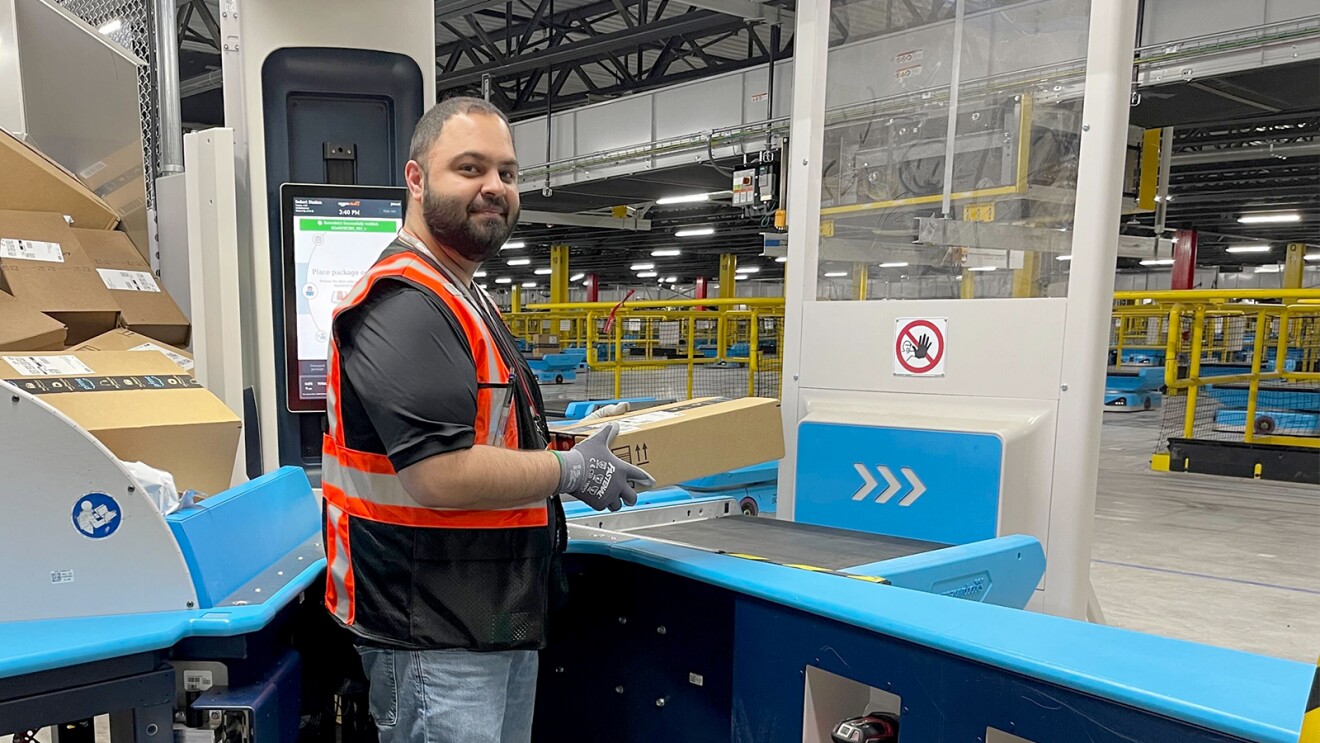
Our robotics fulfillment centers allow us to store millions of items. They serve as distribution centers where employees work alongside state-of-the-art technology to stow, pick, pack, and ship orders seamlessly. Our fulfillment network is integral to our process of fulfilling customer orders around the world. Once a customer places an order, the products are prepared to be packaged and shipped. Amazon employees check and ensure the quality of each item, before it’s shipped and eventually delivered to a customer’s doorstep.
Amazon offers all kinds of jobs for all kinds of people—whatever your background. While our fulfillment centers are home to innovative technology, it’s our employees who bring the magic of Amazon to life. Each day, hundreds of thousands of fulfillment center employees around the world work together to deliver with the efficiency our customers expect.
From the outside looking in, it might be surprising to know some of these jobs exist. Here are a few of the Amazon fulfillment center roles and how they work together to delivery for our customers:
1. Inbound
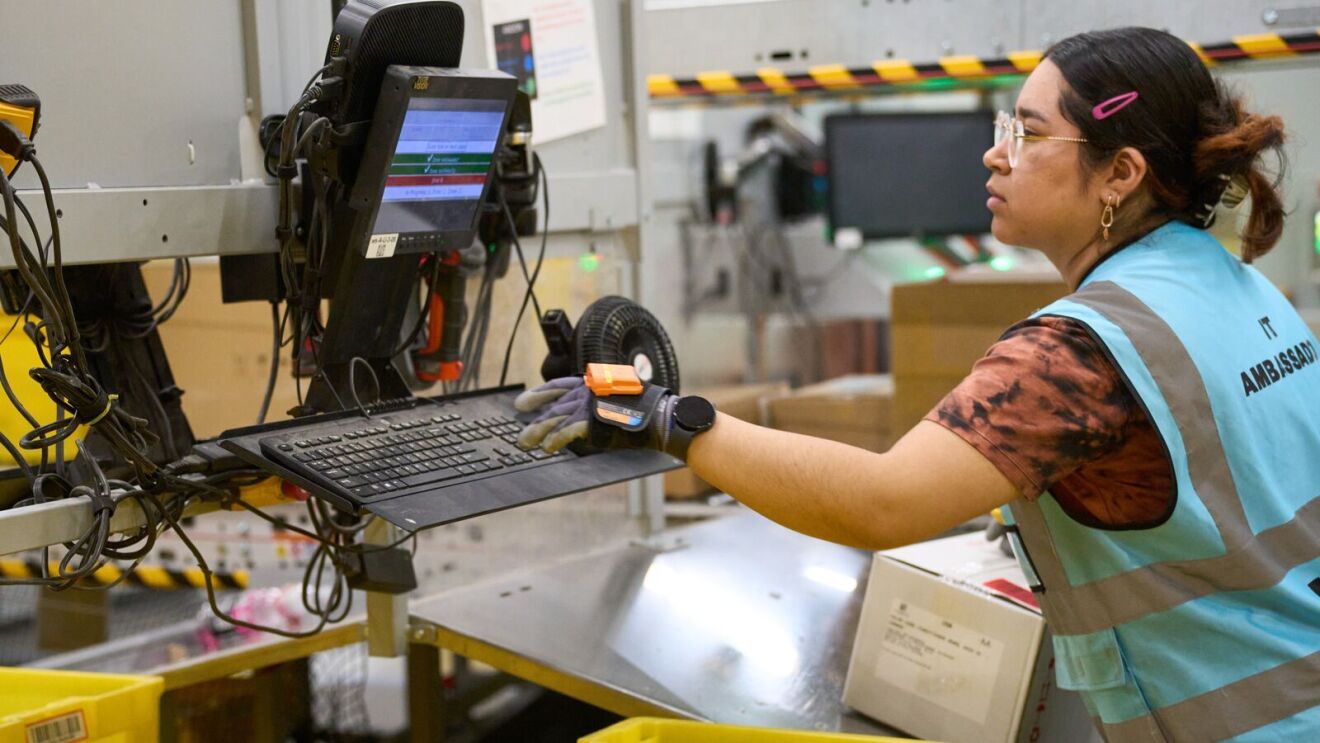
Inbound employees receive products on our loading docks from manufacturers and sellers. These employees unload and unpack pallets and boxes so the items can be easily moved and stored in our inventory for purchase. These teams use our robotic palletizers, which have robotic arms that can build and unload pallets. This simplifies how we move products and eliminates the need for employees to carry heavy items.
2. Water Spider
The term “water spider” originates from the Kanban project management system originally created by Toyota manufacturers. In the Kanban system, a water spider is a role centered around stock replenishment. These employees are responsible for keeping fulfillment center workstations fully stocked. They move products from the inbound area to the stow department and also help keep packing supplies stocked, safely utilizing pallet jacks.
3. Stow
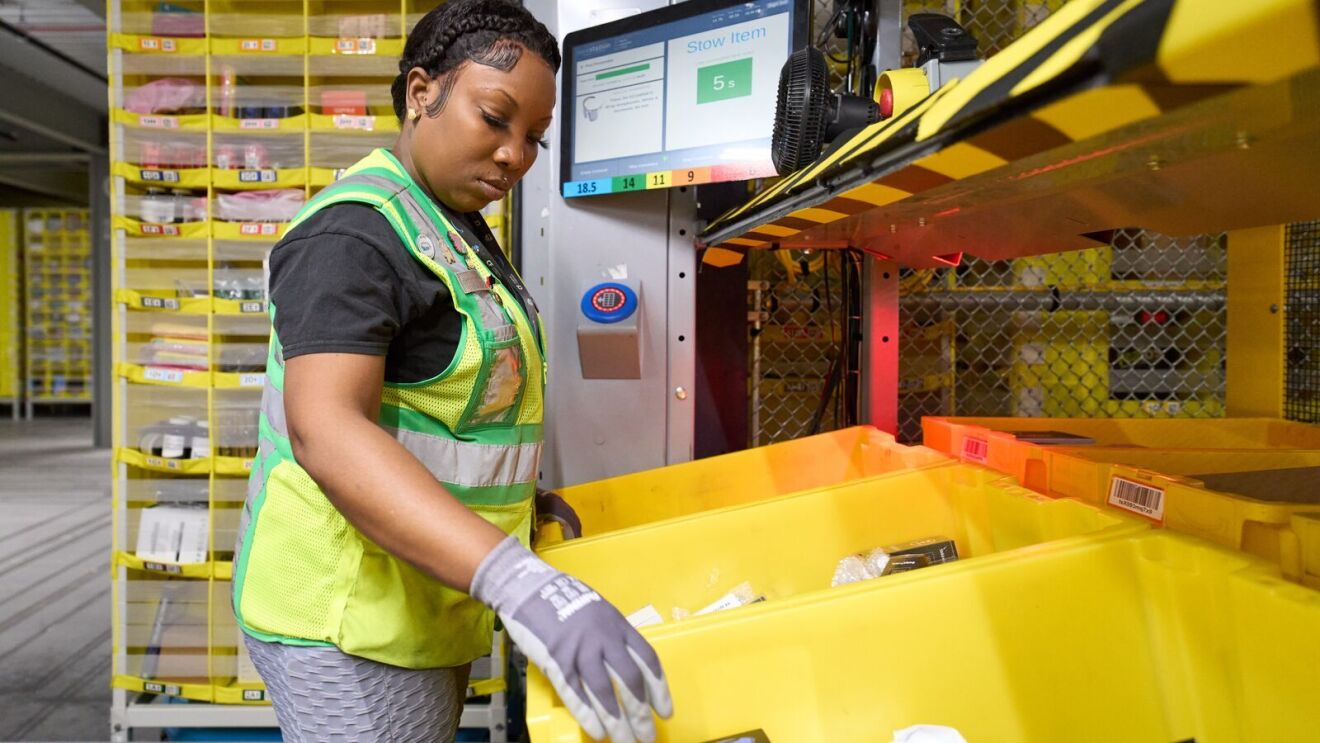
Employees in the stow department interact with enhanced interfaces and technology-driven features to sort and scan products. Once they place items onto inventory racks, they are made available for customers to purchase on our website.
4. Pick
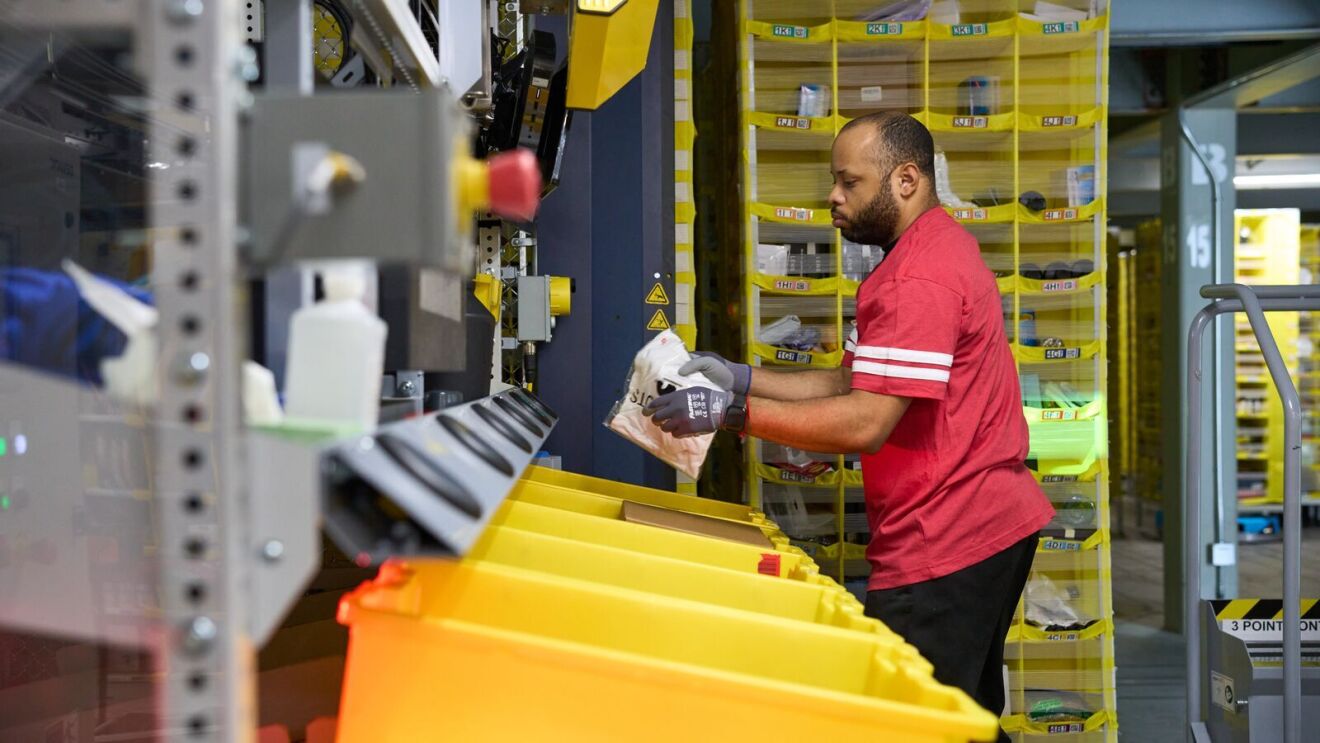
Once an item is purchased, Amazon’s systems cue a robotic drive unit to find the inventory rack where the item is located. Once the item has been found, it's transported to an employee who pulls it off the rack, scans it, and sends it to be packed. Amazon’s stow and pick stations are designed to leverage technologies that work for employees, allowing them to take action based on what the system tells them. These work stations are responsive, user-friendly, and ergonomically designed to keep employees safe.
5. Amnesty
Amnesty responders work closely with robotics technology to problem-solve on the fulfillment center floor by finding any items that fall off the racks and may get in the way of our mobile robots. These employees wear one of our robotic tech vests, which uses advanced technologies, such as AI and sensors, to signal robotic drive units to automatically slow down and update their routes to avoid areas where the employees are working. This continuous stream of information between the robotic tech vests and robotic drive units helps keep our operations moving safely.
6. Pack
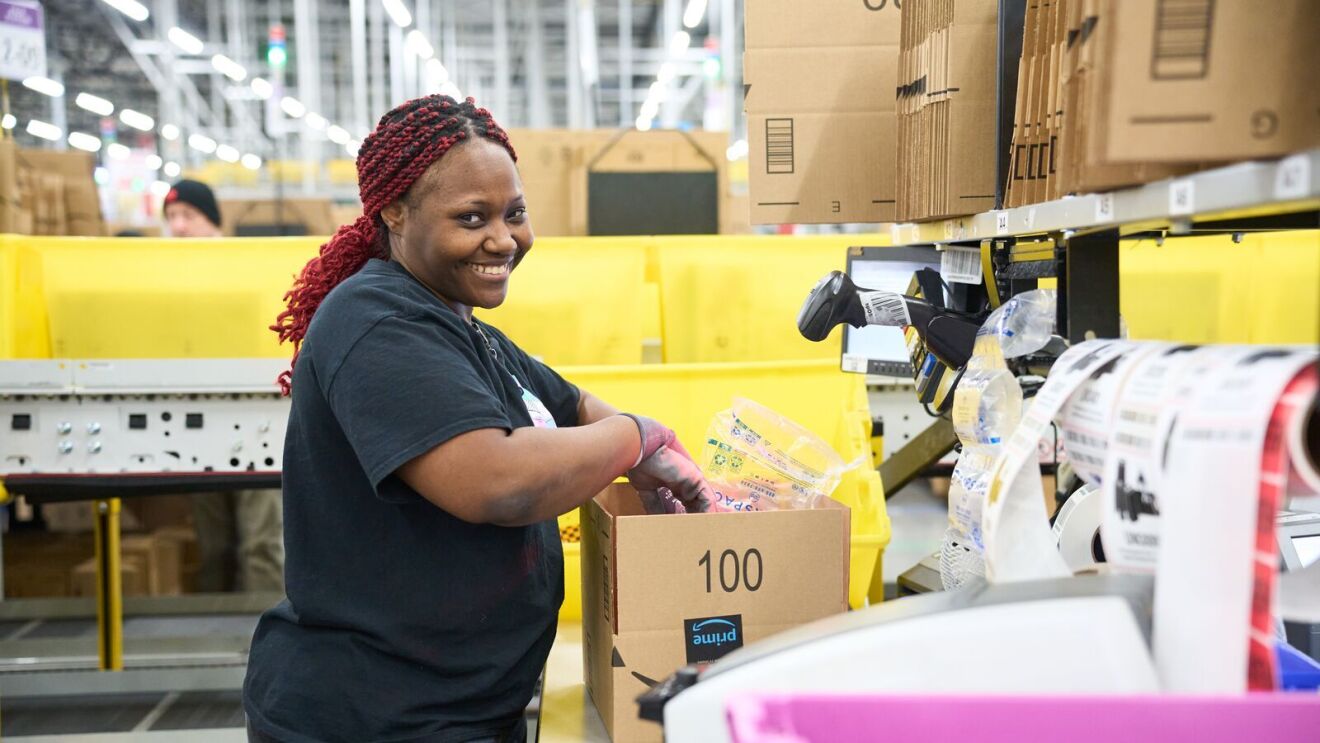
Once an order has reached the packaging area, packers place products into our iconic Amazon boxes or padded envelopes and send them for shipment. Specialized systems notify the employee what size box or envelope to use and what type of padding to include. Another system cuts a perfectly sized piece of Amazon-branded tape and prints a sticker for scanning during the outbound process.
7. Outbound
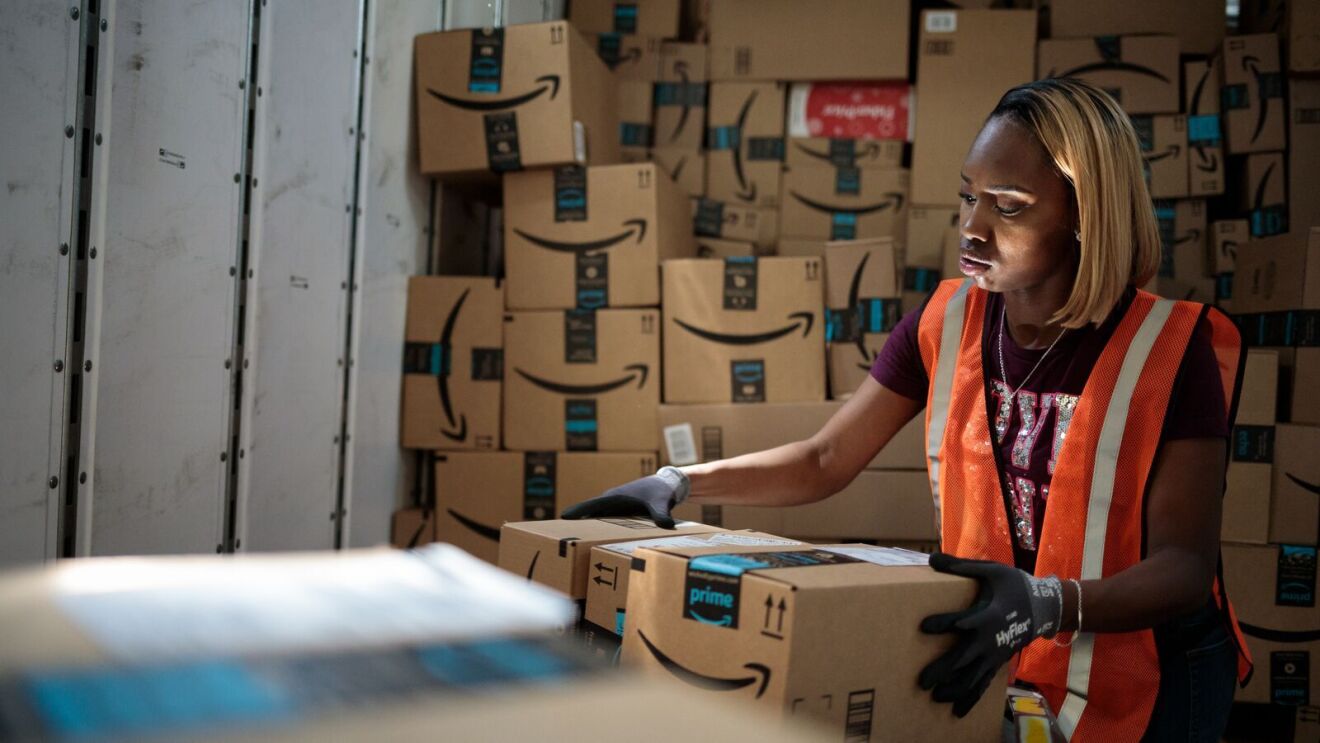
Once an item is ordered, picked, and then packed, it goes to the outbound area to leave the building. Employees who work in the outbound department are experts at packing trucks, working to get boxes of all shapes to fit within the wall of boxes they are building inside the trucks. The boxes are then transported to Amazon delivery stations or carrier partners, where they are delivered to customers’ doorsteps.
What excites me most about our Amazon operations is seeing how our investment in robotics technology has created new types of jobs, made existing jobs safer, and equips us to deliver more efficiently for customers. When I started working at Amazon in 2013, our site had yet to implement robotics technology. Over the years, I’ve seen how this automation has created new jobs, including roles like maintenance technician and flow control specialist.
This past March, I helped lead the team that opened Amazon’s second advanced robotics fulfillment center in the area. As assistant general manager, I like to think of my day-to-day role like that of a pro basketball coach. Each day, I have the opportunity to coach my colleagues and champion their ideas to deliver for my community.
Most of all, I’m proud to have grown my career alongside my father, who also continues his work at Amazon as part of the Reliability Maintenance Engineering team.
Learn more about some of the other leaders and innovators who work at Amazon and explore opportunities at Amazon by visiting our hiring site.
Trending news and stories
- Amazon Pet Day 2025 is coming May 13-14 with 48 hours of deals on pet products and supplies
- LinkedIn names Amazon a top US company where people want to work for the eighth year in a row
- CEO Andy Jassy’s 2024 Letter to Shareholders
- AWS is first major cloud provider to deliver Mistral AI’s Pixtral Large as a fully managed, serverless model