Amazon’s robotics and delivery teams are at the forefront of innovating to deliver a great workplace and customer experience. This week, Amazon invited reporters from around the world to attend its inaugural Delivering the Future event at its innovation labs and robotics manufacturing facility outside Boston, Massachusetts. Journalists got a behind-the-scenes look at the teams and technology that are improving our fulfillment and delivery operations for employees and customers.
Delivering the Future is built on the idea that when people and technology work in harmony, great things happen. It is a future that requires us to invest in our people and their skills, and one where we need to advance fundamental science while remaining practical about how technology can best serve our employees, partners, and customers. This takes shape in many forms—whether that be improvements to how we select, package, and sort items, to how we manage a delivery experience for customers and drivers that is safe, reliable, and sustainable.
Improving fulfillment with automation
A critical part of our fulfillment process happens when employees select inventory—before items are even packaged for shipment to customers. Once the items are boxed up, our existing robotic arms—like Robin and our recently announced Cardinal—can then handle packages in the warehouse before they begin their delivery journey. We saw an opportunity to develop new technology to support individual product handling during the fulfillment stage, which is why we introduced Sparrow, our newest robotic system that significantly advances item handling and how robotic arms can be used in our operations. Sparrow is the first robotic handling system in our warehouses that can detect, select, and move individual products in our inventory. Leveraging computer vision and AI, Sparrow can recognize and handle millions of items. Working alongside our employees, Sparrow will take on repetitive tasks, enabling them to focus their time and energy on other things, while also advancing safety.
Expanding the delivery driver experience
When it comes to customer delivery, the heartbeat of that process is the work of the drivers, who deliver packages on behalf of Amazon. Our custom electric delivery vehicle from Rivian improves the work experience for Delivery Service Partner (DSP) drivers and reduces carbon emissions in the communities where they deliver. These custom vehicles were designed from the ground up with input from DSPs and their drivers to include a suite of innovative safety features like sensor detection, traffic assist technology, automatic emergency braking, adaptive cruise control, and collision warnings. And, with our commitment to have all 100,000 electric delivery vehicles on the road by 2030, Amazon will eliminate millions of metric tons of carbon per year. There is no other delivery van like this in the world.
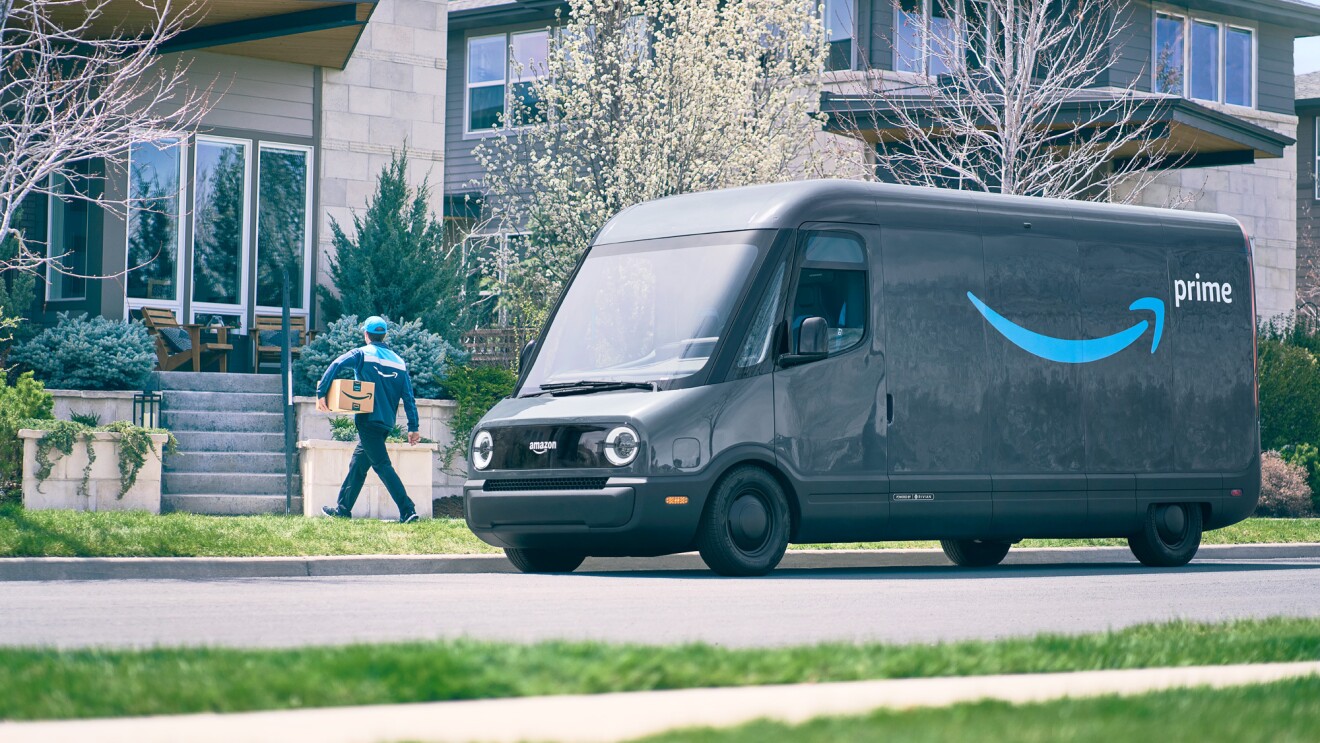
We have learned that the best way to reduce driver-controllable safety incidents is to address unsafe behavior in real time, so we have embedded technology into Rivian and our existing delivery fleet to improve safety. Our best-in-class in-vehicle safety technology identifies safety events. As a result, we have seen a 48% collision rate reduction in our test group since installing it across our existing delivery fleet. We also developed new technology called Fleet Edge, an in-vehicle computer, street-view camera, and GPS device that collects street-view images to refresh on-road information in our mapping software, providing the most up-to-date routing data for drivers delivering packages. We have already added more than 120,000 new signs to Amazon’s mapping system using Fleet Edge. With these combined technologies, we are creating a safer experience for drivers and eliminating our carbon footprint in the communities where we deliver.
Innovating with drones
While we have innovated the standard delivery van, we also have designed and built an autonomous electric drone system through Prime Air that can deliver packages under 5 pounds in less than an hour from click to delivery. We are excited to share more details about our plans for Prime Air, how our approach will make our offering unique, and our definition of drone delivery at Amazon’s scale.
Our definition of scale is delivering 500 million packages by drone to tens of millions of customers annually by the end of this decade. This includes highly populated areas such as Boston, Atlanta, and Seattle, while meeting a targeted level of safety that is validated by regulators and safer then driving to the store. We will take an important step towards that with our newly unveiled next generation delivery drone—the MK30. It is currently being built and is due to enter our expanded service in 2024.
Across Amazon, our collaborative robotic systems and delivery technology are making our workplace more innovative, inviting, and safe—all while helping us deliver for customers. We are excited and motivated to continue inventing and using technology in ways that benefit people most.
Trending news and stories
- How Amazon proved its new delivery drone is safe for takeoff
- Amazon’s AI-powered ‘Interests’ feature automatically finds new products that match your passions and hobbies
- Amazon makes it easier for developers and tech enthusiasts to explore Amazon Nova, its advanced Gen AI models
- How to watch ‘Octopus!,’ coming exclusively to Prime Video