Picture this: You’ve successfully orchestrated the safe landing, loading, and takeoff of a 95-ton airplane. Now you’re standing on the runway with your team, watching that plane soar into the sky, where it will reach up to 35,000 feet on its way to deliver packages to customers across the U.S. This is the moment Ryan Swagler and Jake Rose, leaders on the Amazon Air team, were most looking forward to ahead of the launch of the new Amazon Air Hub in Kentucky.
“One of the best parts of the job is that ‘we did it’ feeling when we watch the first plane fly away,” said Rose, the load planner area manager for Amazon Air. “Just seeing that first plane fly off and knowing that all of our planning and hard work made it happen is exciting for me.”
Swagler, a ramp area manager with Amazon Air, said comradery is a major part of what makes that moment so special. “In my time working with Amazon Air, my team and I have always gotten these big, cheesy grins on our faces when we watch a plane take off,” she said. “Watching the first plane take off from from a new hub is a huge ‘high-five’ moment.”
01 / 02
After building their careers and establishing themselves as skilled leaders at Amazon, Swagler and Rose were selected to be a part of the team leading the launch of Amazon’s new air hub at the Cincinnati/Northern Kentucky International Airport. The hub officially launched this month, and we caught up with them amid the excitement to learn more about their work, their teams, and what advice they have for people interested in similar careers.
Q: How would you describe your role?
Rose: My job at the new hub is to lead the load planning team. So my team is responsible for coordinating a plan to load each plane. This is a critical part of the process because the load plan helps us ensure the plane maintains a stable center of gravity as we load the cans onboard. Cans are the containers we use to pack and load packages onto each flight.
Swagler: I lead the team that does everything on the ramp, which is the area where we bring the planes to load them. My team marshals the planes in, loads them, and pushes them back in preparation for takeoff. It’s exciting work! Though my role focuses on managing the team, I’ve also done training on every part of the job because I wouldn’t ask my team to do anything I wouldn't do myself.
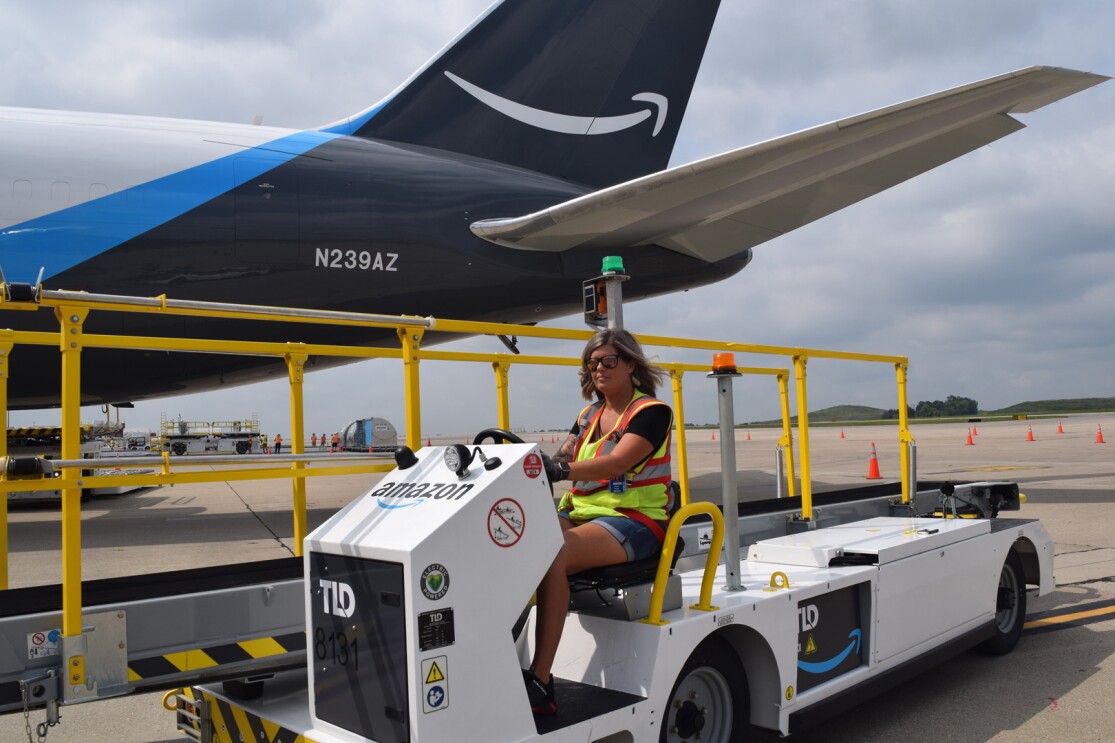
Q: How have you prepared for the launch of the new hub?
Rose: We started by hiring and training our teams. We also prepared by refining our processes to further innovate for safety and efficiency on day one. Part of that meant traveling to other hubs to see how they’re doing things. The whole team visited the Amazon Air Hub in Lakeland, Florida, to learn more about their operation and get familiar with every role and each step in the process.
Q: What goes into the process of loading an Amazon Air plane?
Rose: The process of load planning starts when the first inbound flight of the day comes in. The sort team unloads the packages from the inbound flight and organizes them according to their final destination. The team then loads the packages into the cans for the outbound flights and provides the load planning team with the weight and quantity specs for each shipment. From there, we take that data and add it into our virtual load-planning software to build a load plan for each flight. The load plans are what the ramp team uses to load and crosscheck the planes due to go out. It’s a high level of responsibility and requires a lot of care when it comes to making sure all the weights and info are correct, for both safe and efficient physical loading of the aircrafts.
Swagler: There are more than 100 employees working on the ramp to complete the unloading and loading process, which takes about two hours total. It starts with the team that marshals the plane in from the runway to its assigned parking spot. From there, we set up all of the equipment, and another team on the ramp starts the process of unloading the cans of packages that are coming into our facility. Then a specially designed truck comes in to grab and haul those cans from the K loader, which is a large elevator-like platform that helps unload the plane, and takes them into the building. Once the sort team packs the packages into cans, the same trucks—driven by what we call tug drivers—bring the cans out to the plane. After the ramp team has loaded each can in its specific spot, we check to make sure that it's loaded properly and according to the load plan so the plane flies safely. Then we push that plane back and follow it through to takeoff.
01 / 12
Q: What was it like to work with a plane for the first time?
Swagler: When you first go out there and stand next to a plane, it’s amazing to see how small you are in comparison. I was really intimidated when I first saw it, but it was a lot of fun, too. Not everyone gets to work with the incredible machines, and it’s such a cool opportunity to work so closely with them and learn so much in the process.
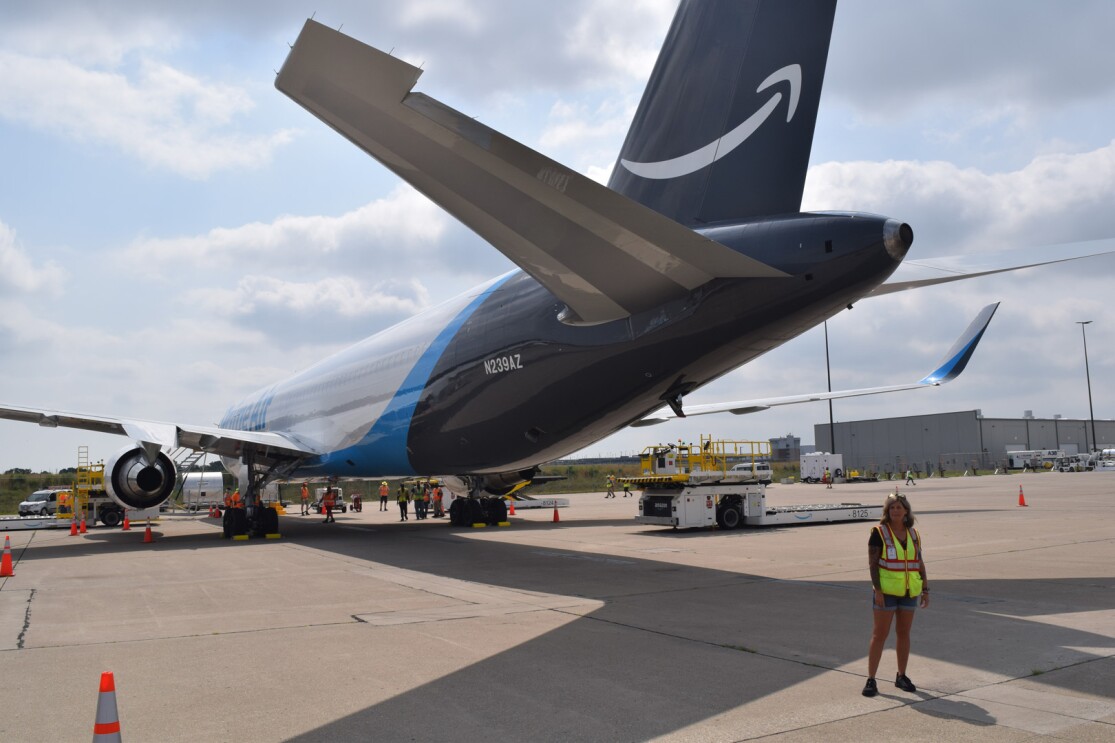
Q: What is your favorite part about leading a team at Amazon?
Swagler: My favorite part of my work is watching my team “fly high.” I know it sounds cheesy, but that’s what we say in air, and it’s actually perfect when you consider the context of the job. Most of our employees have never worked with planes before, and we take them through the training and watch them grow to the point where they get to watch their first plane take off. You can see the sense of accomplishment in their eyes. It’s amazing to watch others succeed.
Rose: I'm excited to be that person to help support my team and give them what they need to be successful in their roles. I’ve been in their shoes before and feel confident in my knowledge of the process, so it’s exciting to anticipate the team’s needs and get them set up for success.
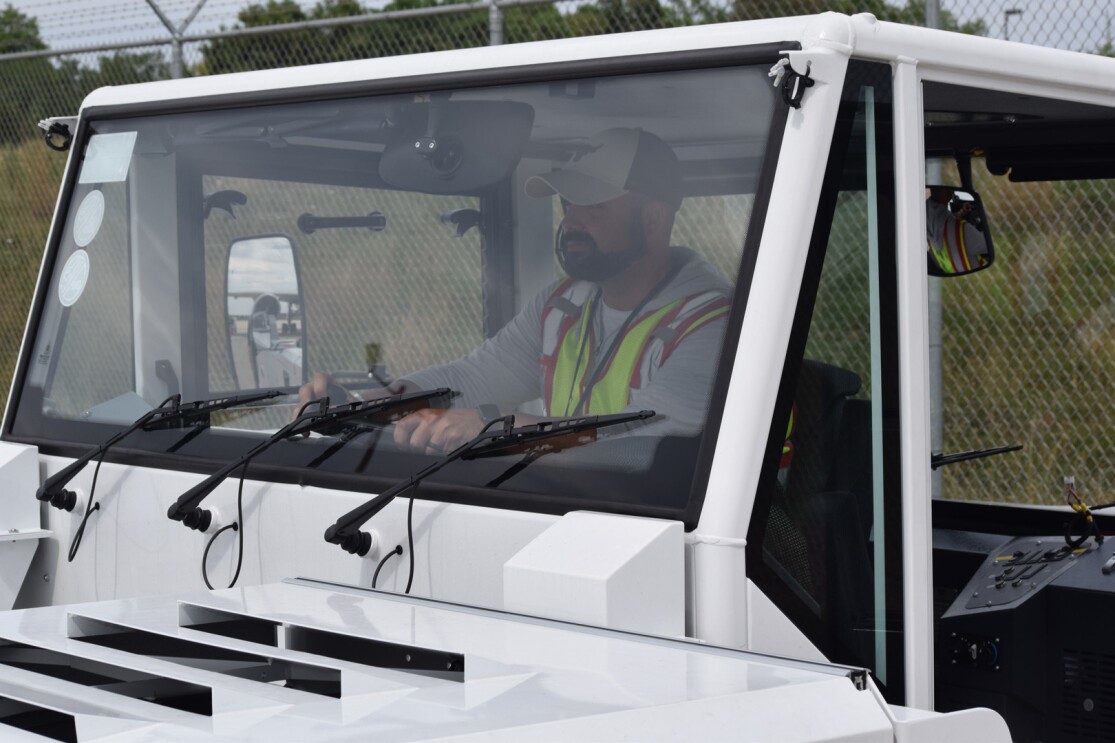
Q: Every step in the process of your work is so critical. How do you cultivate the teamwork necessary to pull it all off?
Rose: There’s something about working at an air hub that inspires comradery and gets you into a team-orientated mindset. It’s like a pit crew mentality—everything becomes a beautiful chaos once the plane touches down, and all of the planning and processes fall into place to get the job done. Everything about working with airplanes is just amazing, and I think the fact that every role and every step is so important helps the team feel valued and connected to accomplishing a greater goal.
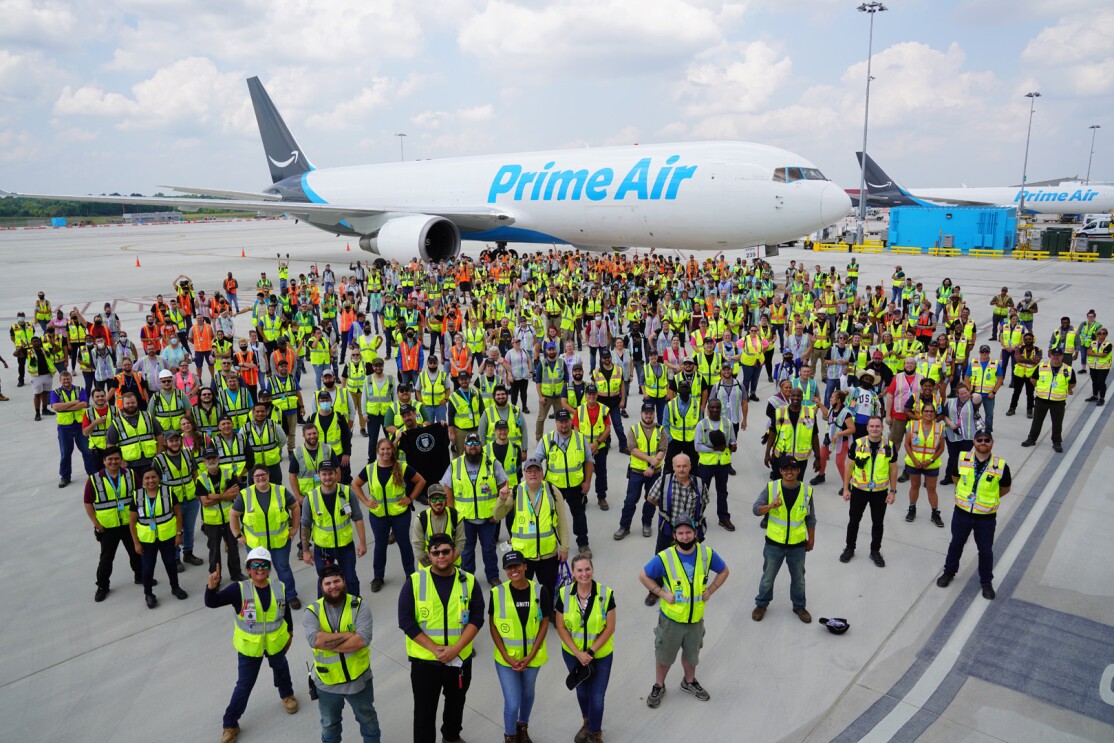
Q: What goes into the process of training to work on the Amazon Air team?
Swagler: When you start in a planeside agent (PSA) role, you go into training for about two weeks. These are full-day trainings where you learn the important tasks of your role and, most importantly, how to do them safely. The first week is a class and the second week is on-the-job training with a real plane. Our ramp associates train with ambassadors planeside, going through all the daily job duties for one week. If there is a process someone is struggling with toward the end of the training, leaders will work with them to shadow someone with that job for a while to ensure they get the process down before they start working with planes. Once a PSA is ready to join a team, we assign them to a ramp crew where they get on-the-job training.
Q: What advice do you have for others who aspire to a career like yours?
Rose: Set a goal and go for it. I was in shipping for many years and I knew that frontward and backward—it was my safe place, really. I wanted something different so I made a goal to learn and be curious. When I started exploring new opportunities to learn and grow at Amazon, everything just kind of soared. Everything I wanted just fell into place. Goal setting is especially helpful for those who are already working at Amazon. If you have a goal you’re after, Amazon's going to help you get there, and so will your colleagues. I had great mentors who helped me get to where I am.
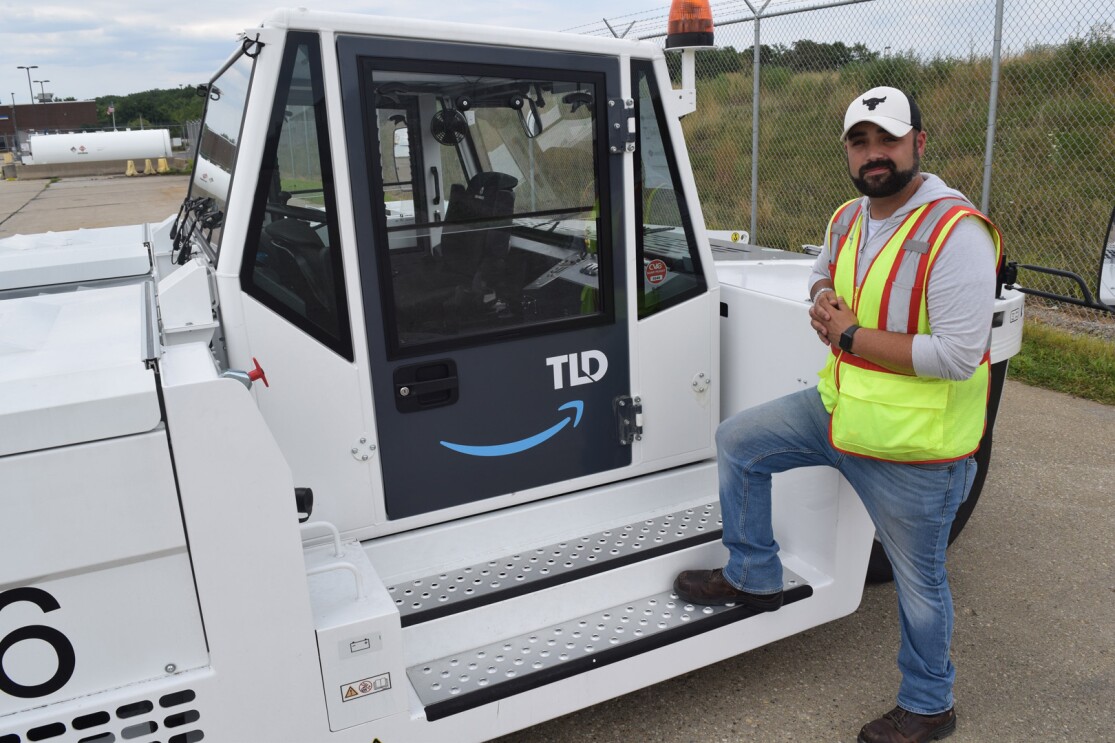
Swagler: Never be afraid to learn, never turn down an opportunity to grow, and always make yourself available to take on projects. It’s important to take every opportunity to let yourself shine. It’s easy to get complacent—doing the same thing every day can be very comfortable. There’s nothing wrong with feeling comfortable in your job, but pushing yourself to learn new things is what will keep you moving forward and show others that you deserve more opportunities.
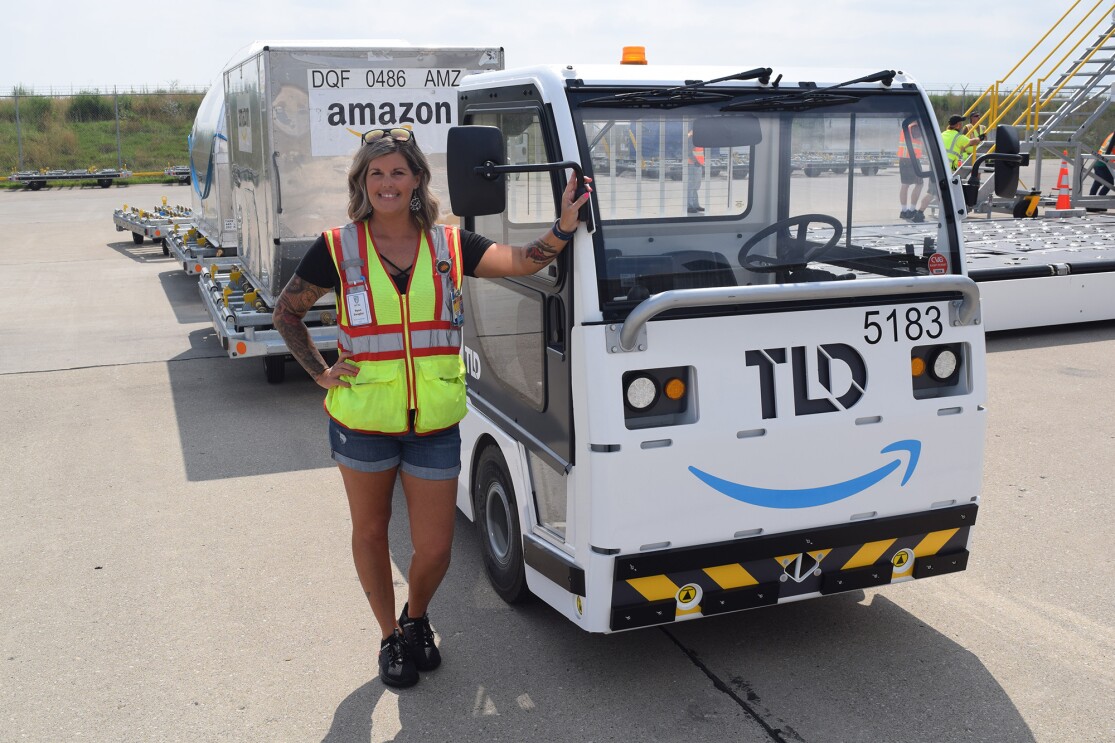
If you enjoyed learning about Swagler’s and Rose’s real (cool) jobs at Amazon Air, read more articles from this series. For more information about opportunities at the company, visit Amazon.jobs.
Trending news and stories