The construction industry is one of the largest and toughest sectors to decarbonize. Embodied carbon—the emissions released during building materials’ life cycle, from extraction to manufacturing, transport, and construction to disposal—accounts for around 11% of global carbon emissions.
As part of The Climate Pledge, Amazon and Amazon Web Services (AWS) are focused on increasing energy efficiency, expanding the use of renewable energy, and reducing the embodied carbon of our infrastructure to reach net-zero carbon by 2040.
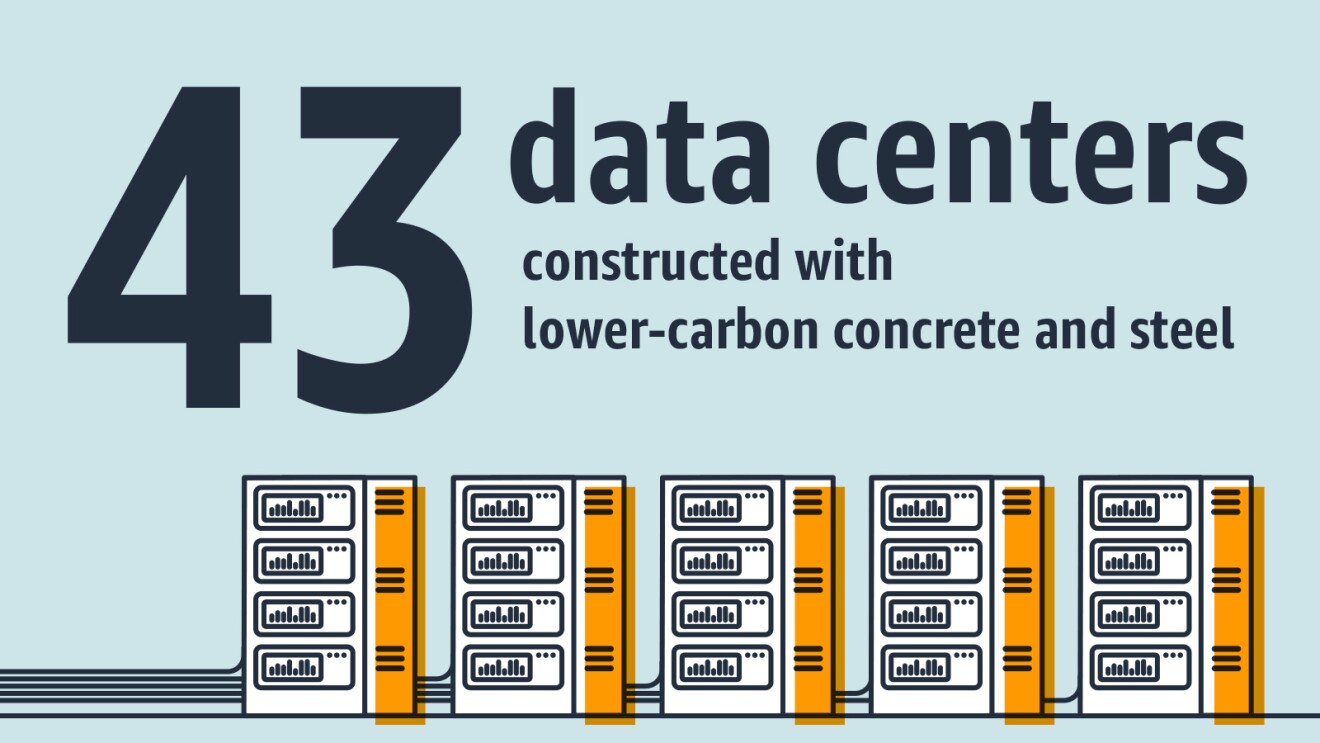
AWS is working across our supply chain to build data centers with lower-carbon concrete and steel wherever possible. AWS has 43 data centers across the globe that have been constructed with either or both lower-carbon concrete and steel—more than double its previous reported total in 2022. So far announced in this year, we've saved more than 22,000 tons of carbon dioxide equivalent (tCO2e) from the construction of 27 data centers using lower-carbon steel and concrete. That’s the equivalent amount of carbon emissions resulting from charging more than 2.6 billion smartphones.
Here’s how we are continuing to drive progress on this effort.
1. “Designing-out” the overall amount of steel and concrete we use
We continuously evaluate the design criteria for everything from server racks to office spaces and storage rooms. Doing so allows us to find opportunities to reduce the total amount of materials, like steel and cement, needed to support our buildings. We recently identified an opportunity to change the air system in our data center designs to reduce the amount of materials we use in new building structures. By removing the concrete topping from a mezzanine floor and only using steel beams, we save roughly 115 metric tons of carbon dioxide equivalent per data center.
2. Testing lower-carbon cement alternatives
Cement is responsible for roughly 90% of the embodied carbon in concrete. One way manufacturers are developing concrete mixes with lower embodied carbon is by incorporating recycled byproducts (such as slag, a byproduct of smelting ores and recycled metals) from other industrial processes to replace ordinary cement. Another solution is to replace ordinary cement with Portland-Limestone Cement (Type IL), which contains a higher ratio of raw limestone to ordinary cement and a lower embodied carbon. When used in combination, these two methods can reduce carbon emissions by up to 50%.
One of the largest barriers for suppliers to adopt these lower-carbon alternatives is the confidence that the cement substitutes won’t compromise the construction schedule, ease of placement, or final appearance of the concrete. We’re working with suppliers, including Ash Grove, Holcim, and Titan America, on testing the mixture to ensure strength and performance standards—such as water-to-cement ratios, air content, and shrinkage limits are satisfied. This is known as “trial batching.”
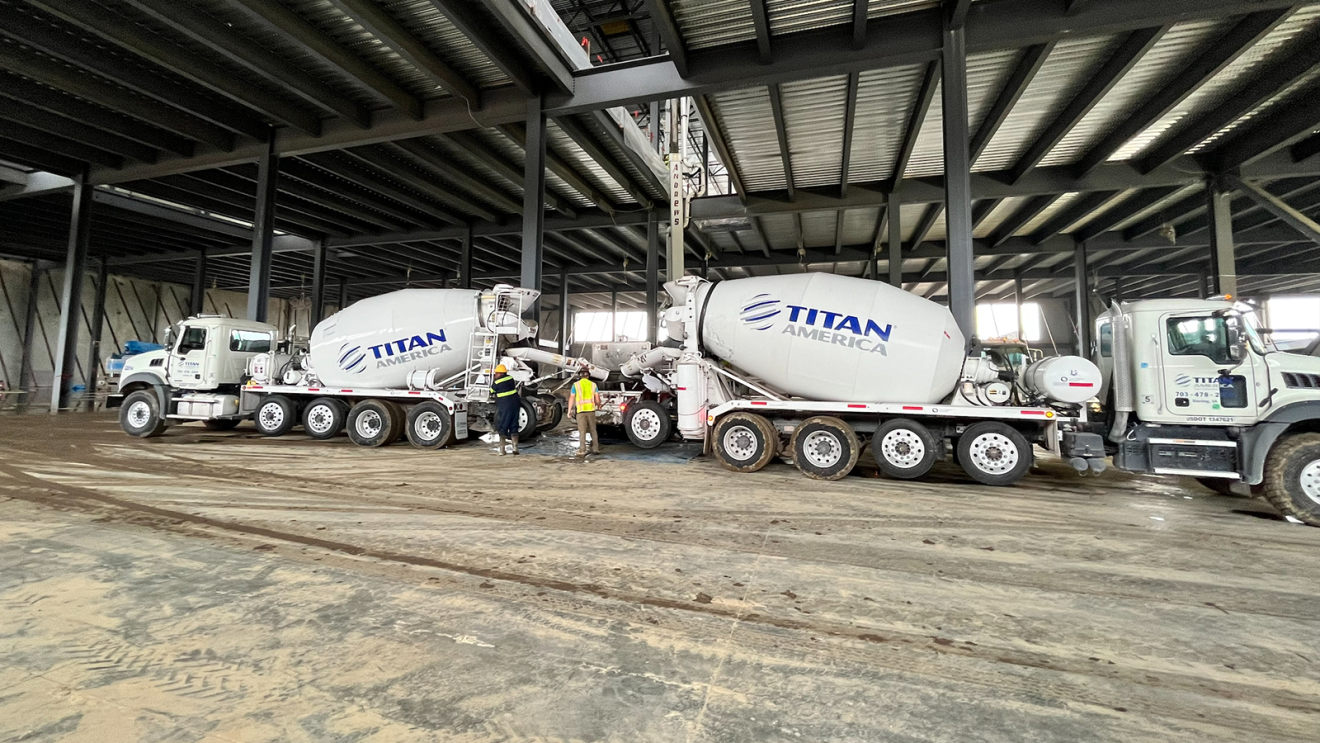
After trial batching a mixture for a data center construction project in northern Virginia, our concrete supplier was able to replace 40% of the ordinary cement with slag, while still meeting the project’s schedule constraints. Thanks to the reduced cement content, we cut embodied carbon in the cement mix by more than 30%.
“Developing the right combinations of lower-carbon cement materials while maintaining performance and construction schedules can be a challenge,” said Eric Koehler, vice president of Innovation and Quality at Titan America. “We're collaborating with AWS to test and deploy options to identify and scale effective concrete mix designs.”
We’re working with iMasons Climate Accord, its members, and the broader industry to help accelerate and expand the availability of lower-carbon concrete for other companies constructing data centers worldwide.
3. Encouraging our suppliers to incorporate lower-carbon steel into their supply chains
Globally, the most popular manufacturing method for steel is the basic oxygen furnace (BOF), which burns coal or gas. But rather than relying on fossil fuels, steel can also be produced in electric-arc furnaces (EAF) that use scrap steel and are powered by energy from the grid—in some cases from renewable sources. In 2021, we began purchasing EAF steel for data centers, which commonly amounts to half of the embodied carbon compared to BOF steel production, and can even achieve as low as one-fifth.
Another way to reduce the carbon footprint of a data center is by using higher-strength structural steel, made by cooling the metal quickly during manufacturing. This gives the steel a higher strength-to-weight ratio, allowing a smaller quantity of material to deliver the same function, without increasing the embodied carbon. By incorporating higher-strength steel into our structural designs, we’ve achieved a weight reduction of 70 tons of steel for each two-story data center.
4. Investing in innovative technologies to drive carbon reductions in the future
We’re always looking for the best available technology to decarbonize the data centers we build today, as well as those we’ll build in years to come. Popular cement replacements, such as slag, are byproducts of coal-fired manufacturing, and the supply of these replacements will dwindle as the world transitions away from fossil fuels.
Amazon is helping to bridge the innovation gap by investing in lower-carbon concrete and steel technologies through the Climate Pledge Fund, a $2 billion venture investment program supporting the development of sustainable technologies and services that will enable us to meet our net-zero carbon goal.
Among the early-stage companies that we've invested in is Brimstone, a startup that is developing the first carbon negative process for cement manufacturing, which starts with carbon-free calcium silicate rock instead of limestone. Another is Electra, a company that produces iron at lower temperatures using low-grade iron ores and renewable energy. We intend to use innovative materials like these when they become technically viable and commercially available, and we’ll continue investing resources to support their development.
At AWS, and all of Amazon, we’ll continue to collaborate across our supply chain to design and construct our data centers with the environment in mind.
Trending news and stories
- Amazon Pet Day 2025 is coming May 13-14 with 48 hours of deals on pet products and supplies
- LinkedIn names Amazon a top US company where people want to work for the eighth year in a row
- CEO Andy Jassy’s 2024 Letter to Shareholders
- AWS is first major cloud provider to deliver Mistral AI’s Pixtral Large as a fully managed, serverless model