Amazon recently welcomed nearly 100 reporters from around the world to take a rare look inside the Amazon Global Robotics facility in Westborough, Massachusetts. I tagged along with the About Amazon team and got an eyeful of all the technology the company is developing. One of the coolest things I experienced was a behind-the-scenes tour of how fulfillment center robots are made and tested.
Keep reading to find out what I learned about where these robots come from.
Amazon operates the world's largest fleet of industrial robots. Erika McClosky, director of global robotics manufacturing at Amazon, was kind enough to walk us through the process of building these robots at her facility in Massachusetts.
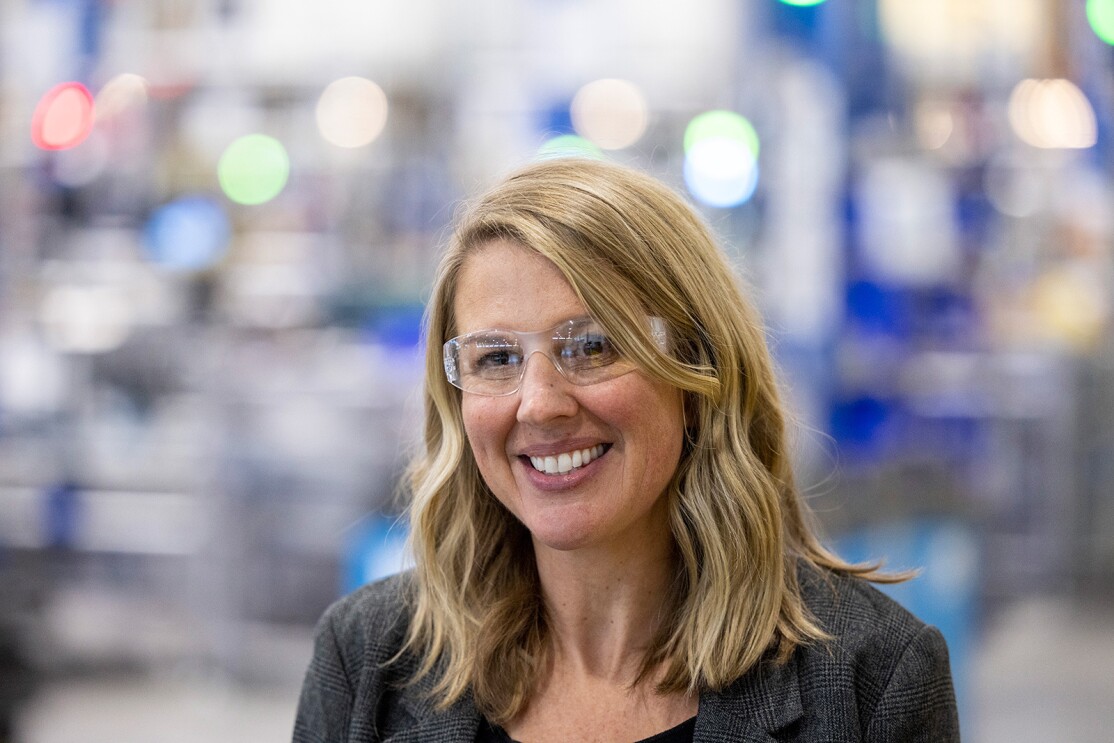
Of course, safety comes first. Before we could step onto the manufacturing floor, our group threw on a pair of safety glasses.
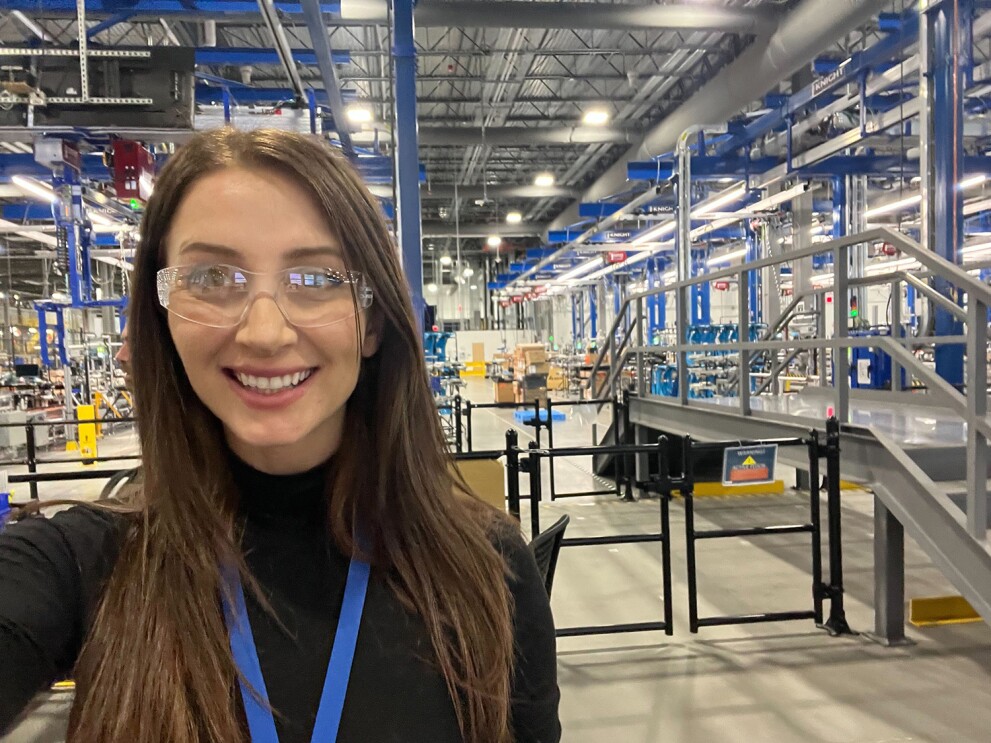
And I happily traded out my high-heeled boots for a pair of comfy safety shoes. (Thank you for the loaners, Erika!)
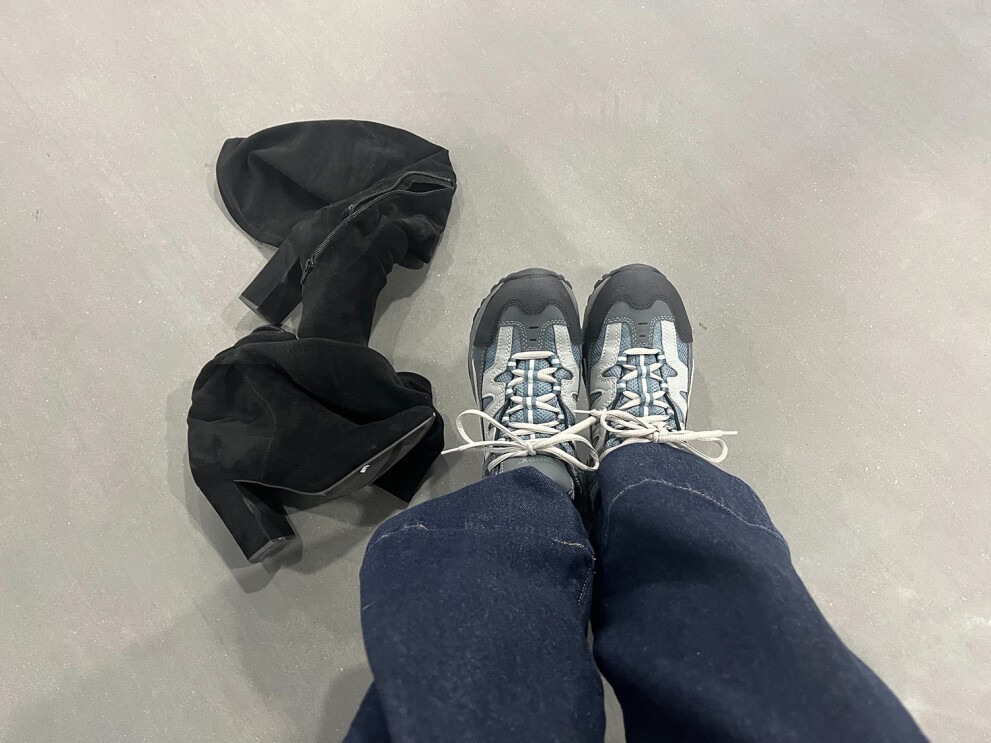
McClosky explained that we would be seeing the process of building a Hercules robot. The aptly named robot is the flat, blue machine that drives around in dedicated areas of our fulfillment centers to lift and carry products.
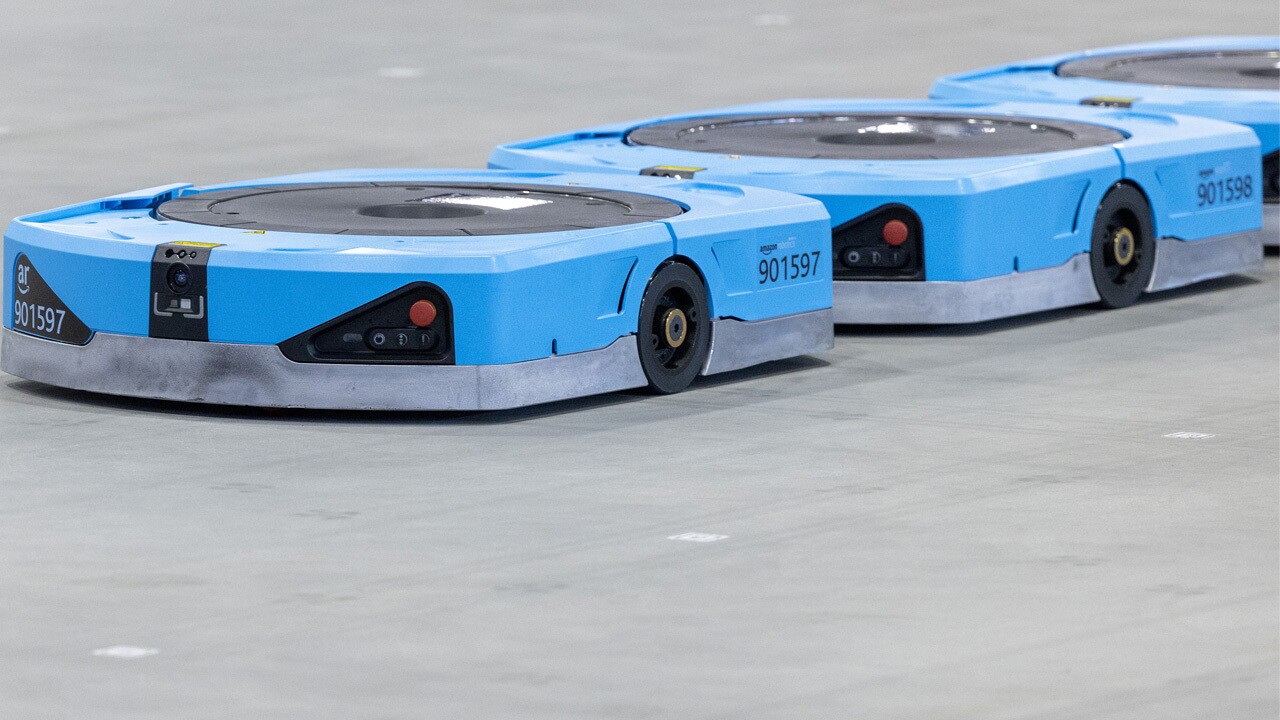
Each assembly line starts with a large, claw-like robot. The claw lifts the heavy base plate of the Hercules bot onto the conveyor belt so assembly-line employees avoid strain.
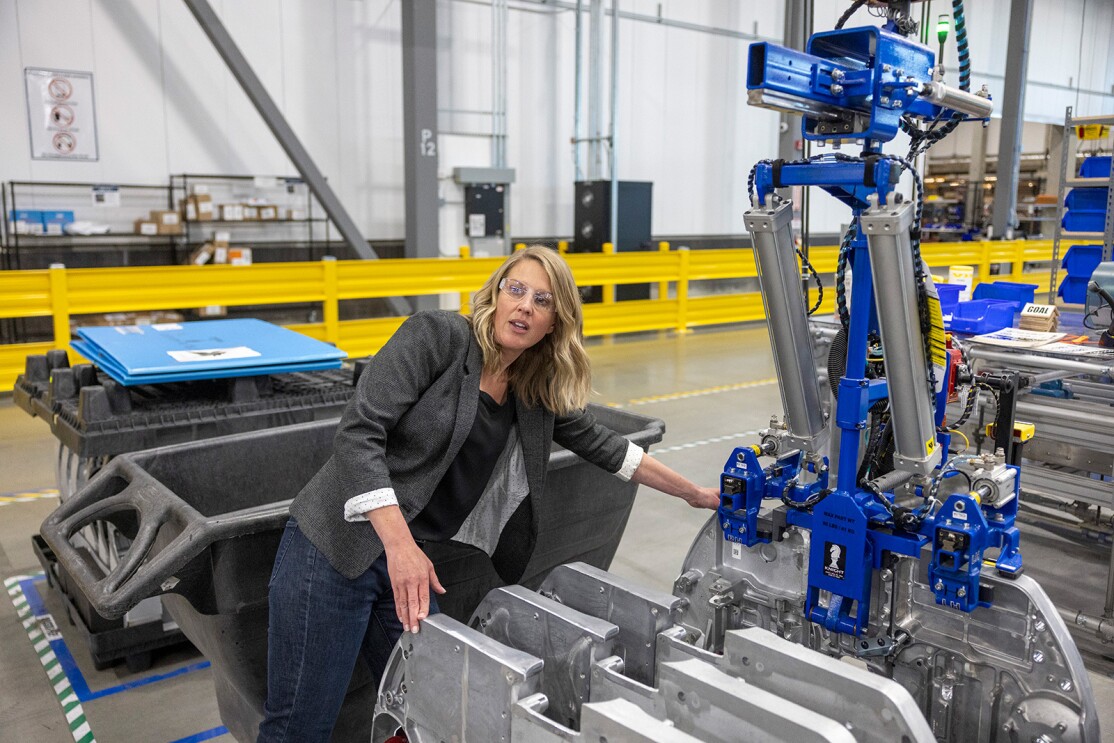
There are 10 stations on each line, and employees at each step perform different parts of the assembly process, slowly bringing the robot to life.
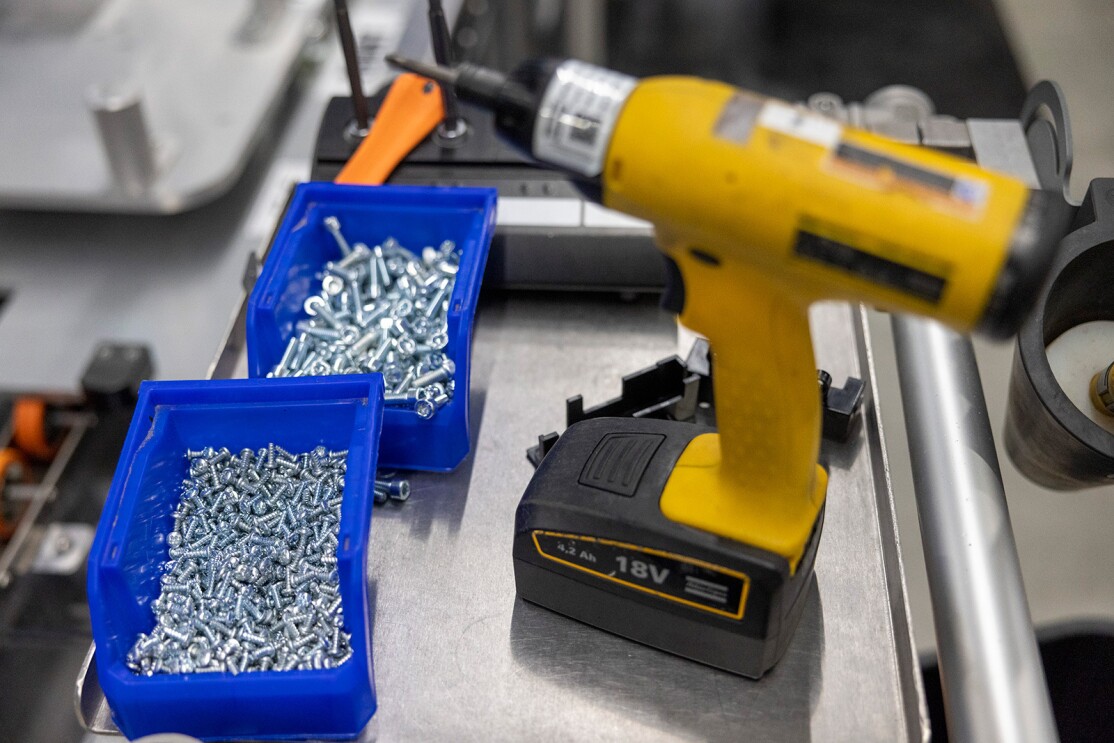
Every station has a screen of instructions so employees know exactly what to do as they move from station to station throughout the week. Each task takes about six minutes to complete.
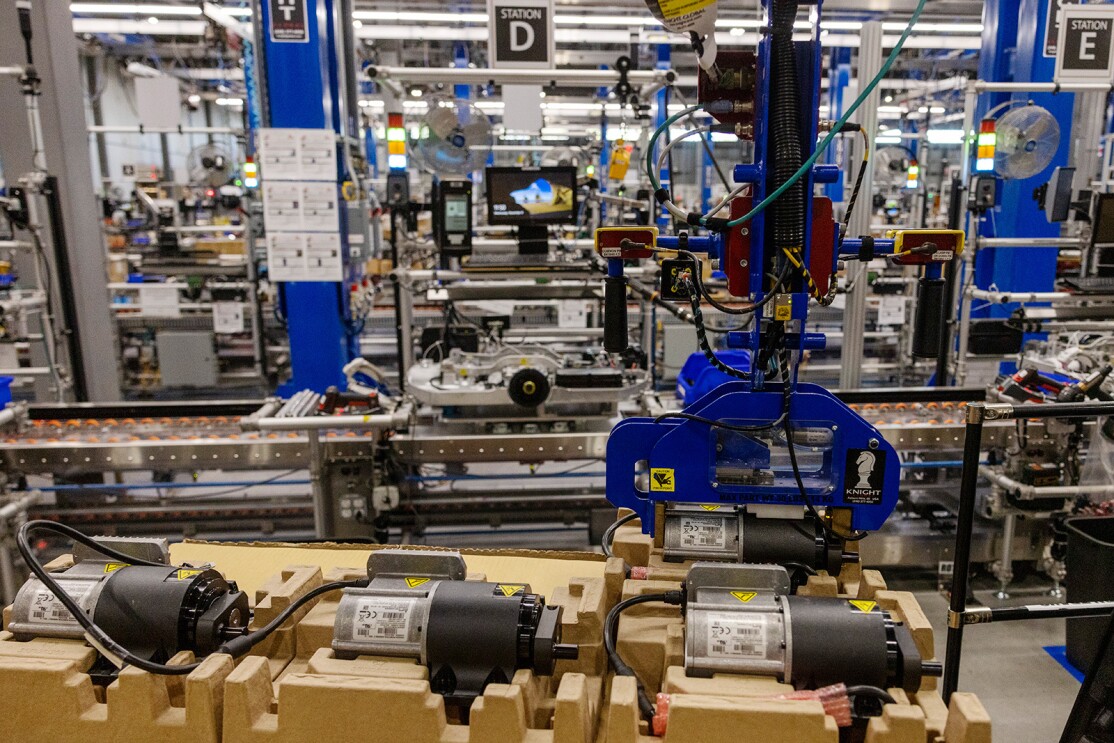
The assembly process takes about an hour for each robot, including a functional test at the end of the line. We can produce up to 1,000 robots each day.
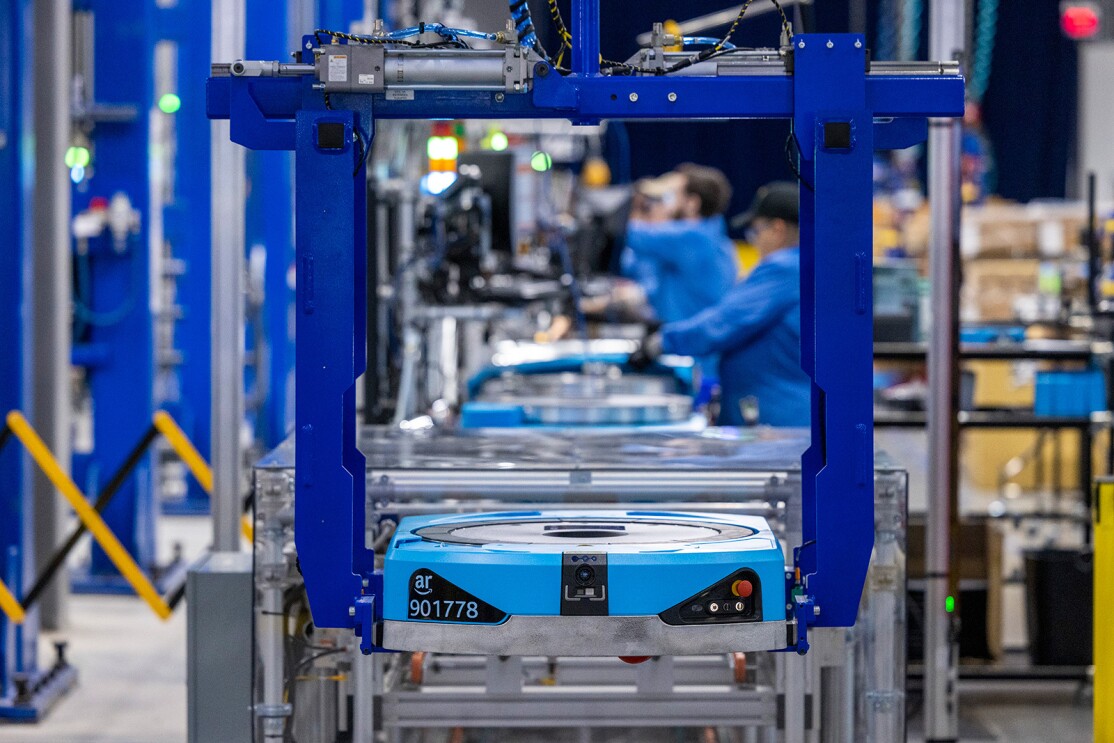
Another claw-like piece of equipment is used to pick the robot off the assembly line and place it on the facility floor. From there, the robot drives itself to a separate area to receive a charge and start the second phase of testing.
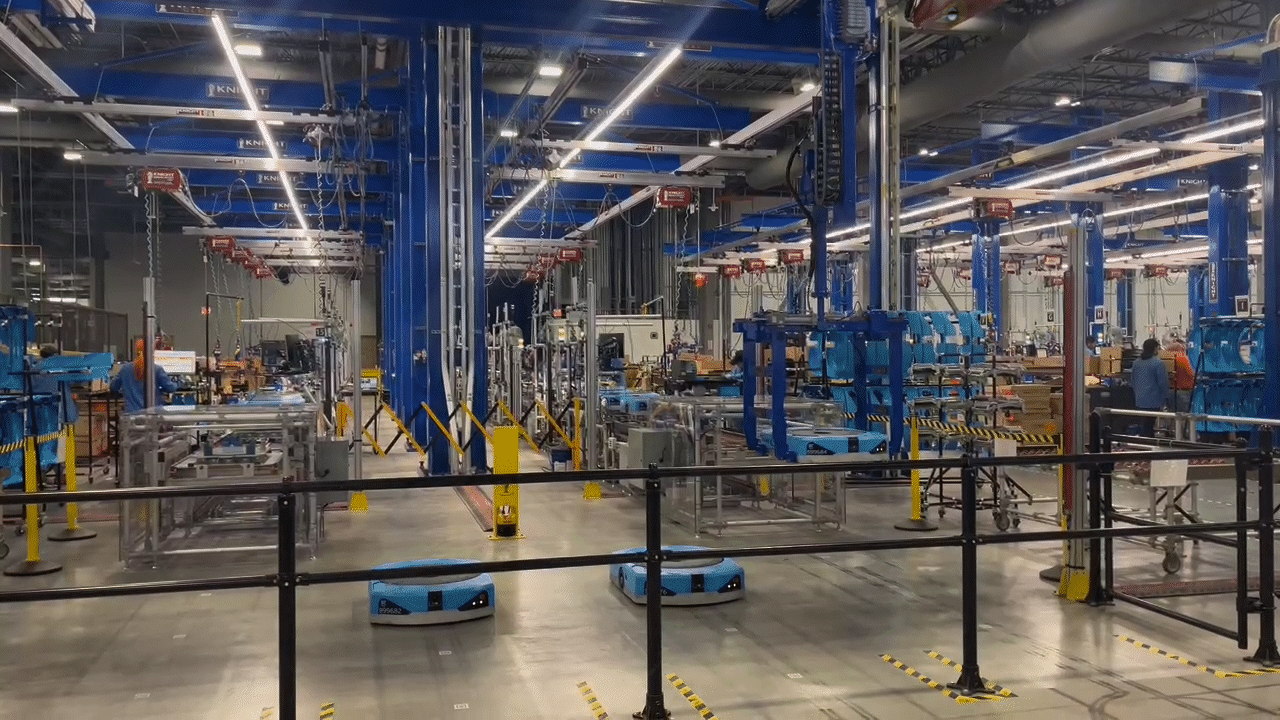
The big, blue boxes you see at the edges of the testing area are called drive unit verifiers. The robots drive themselves into the verifiers to simulate their work at fulfillment centers.
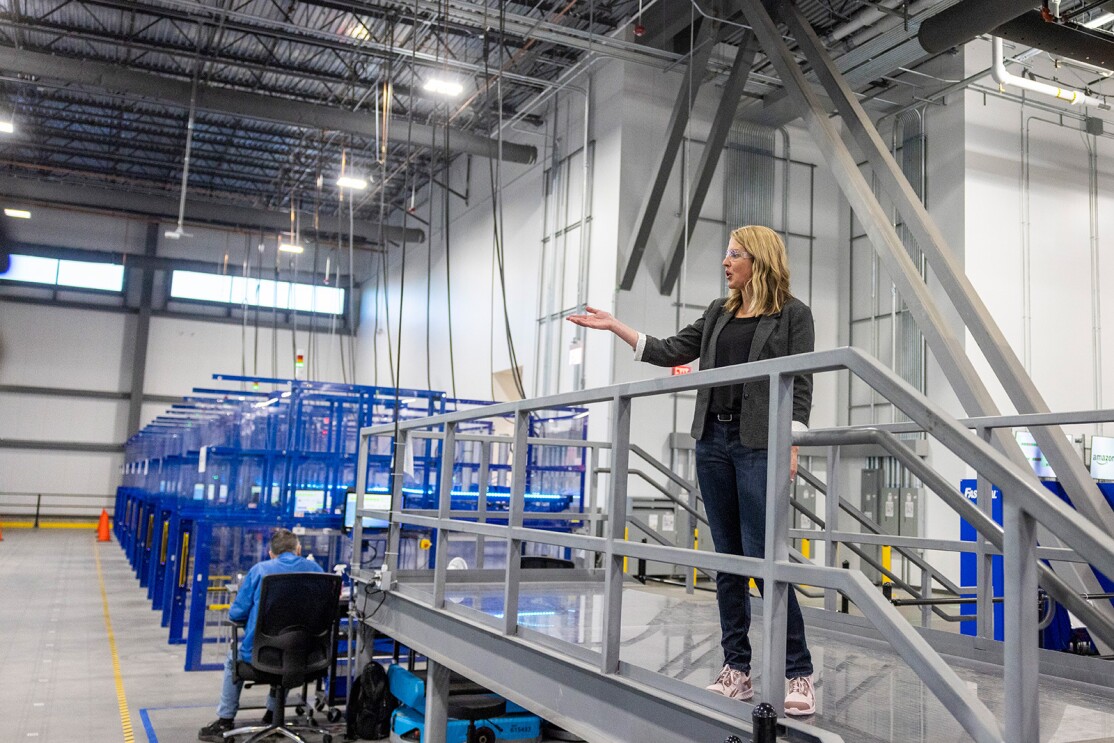
The drive unit verifiers make sure each robot is able to lift hundreds of pounds—a required capability for its future job. Fun fact: McClosky said employees voted to name the verifiers after superheroes.
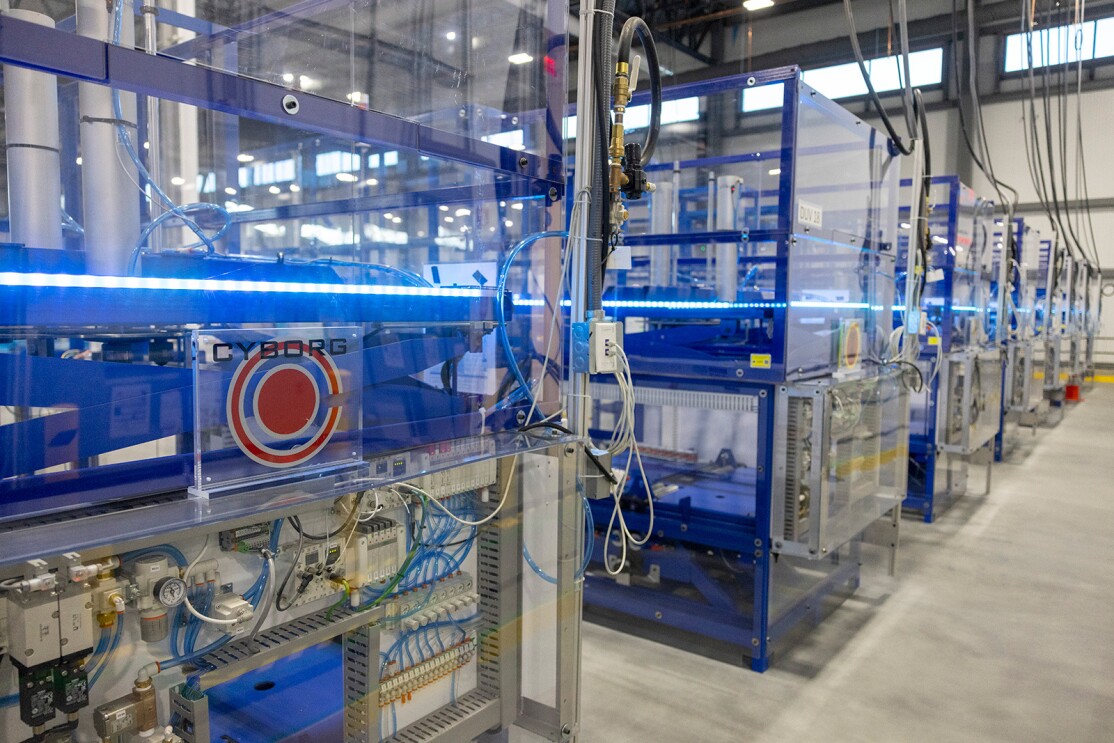
Once testing is complete, the robot drives itself to obtain another charge and loads itself onto a pallet to be packaged and shipped to a fulfillment center.
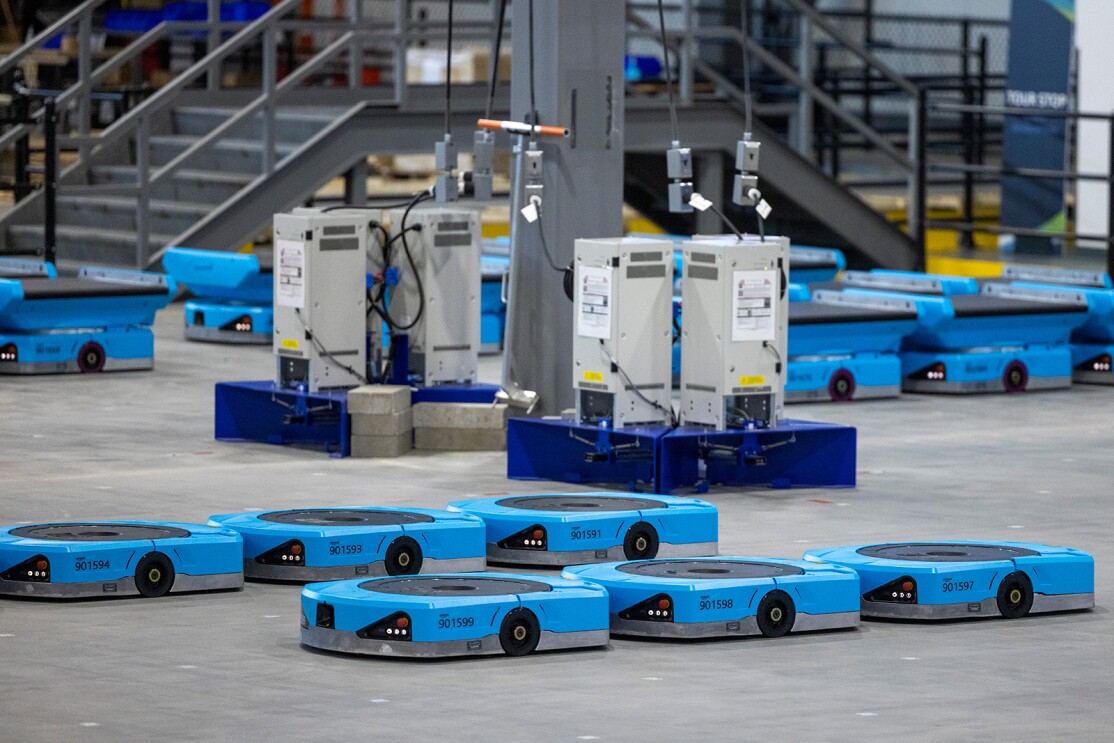
We asked around to make sure the robots go to loving homes. Operations manager, Kory Sellers, assured us that Hercules is among the most beloved robots at his facility in North Carolina.
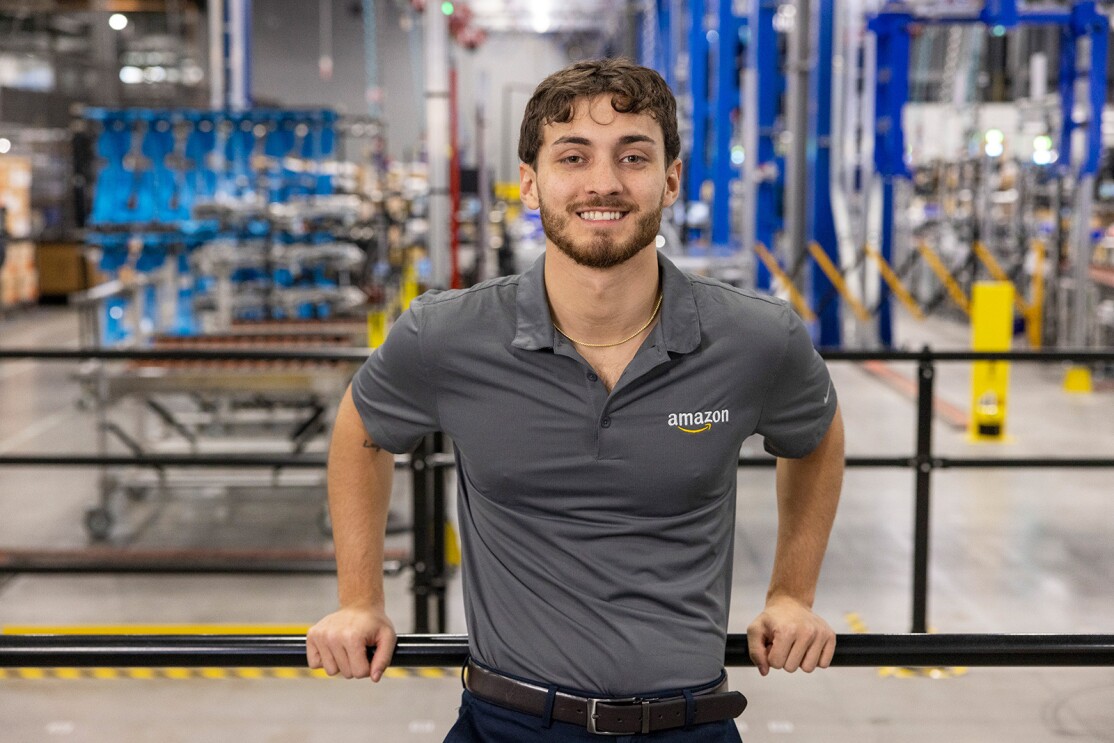
And that, my friends, is how an Amazon robot is brought into this world to help make employees’ jobs easier and safer at our fulfillment centers. Learn about some of the newly announced robots that will be joining Hercules on fulfillment center floors soon.
Trending news and stories
- CEO Andy Jassy’s 2024 Letter to Shareholders
- AWS is first major cloud provider to deliver Mistral AI’s Pixtral Large as a fully managed, serverless model
- Amazon VP shares his approach to the future of robotics innovation
- Amazon Pet Day 2025 is coming May 13-14 with 48 hours of deals on pet products and supplies