Paul Palcisco spent the last 20 years building things that fly fast and high. Now he’s taking his game to a new level.
Before joining Amazon, Palcisco built aircraft engines at GE for most of his career—including the most powerful jet engine in the world. Last year he joined Amazon’s Project Kuiper and set his sights even higher. Project Kuiper is Amazon’s bid to build, deploy, and operate a constellation of satellites in low Earth orbit.
These satellites will deliver fast, affordable broadband to communities around the world, including those that have been historically underserved. The program just announced plans to expand manufacturing with a new satellite production facility in Kirkland, Washington.
“There's a significant portion of the population of the world who don't have access to the internet today or has very slow access,” said Palcisco, who serves as Kuiper’s director of production and leads the Kirkland plant. “When we think about the advantages good connectivity to the internet can provide, the impact on people's lives is tremendous.”
Out of this world
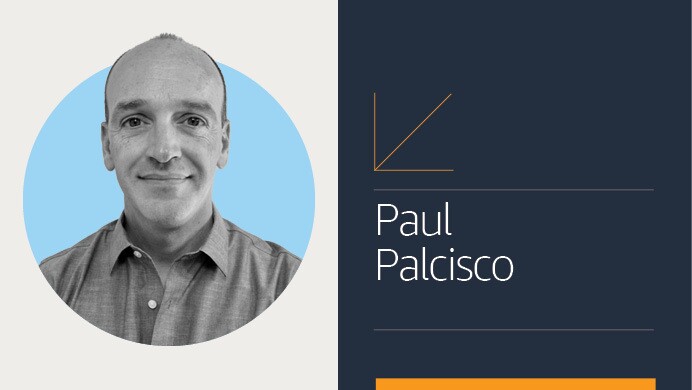
Building space satellites isn’t for the faint of heart. Unlike a car or even a jet engine, you can’t simply bring them in for service. They must be tough enough to survive in space, and they must be built to near-perfect specifications.
The satellites Palcisco and his team are building will live in the low Earth orbit, at altitudes between 366 miles and 391 miles, and reach speeds of 17,000 miles per hour. It’s an extreme environment: Every 90 minutes or so, temperatures swing between 100 degrees and minus 50 degrees Celsius (or 212 degrees to minus 58 degrees Fahrenheit) as the satellites zip around the planet, from shade into the sun’s glare and back. They must also withstand cosmic radiation, solar storms, micro meteorites whizzing by at thousands of miles an hour, and other cosmic perils.
But first, the satellites have to reach this inhospitable place with their delicate instruments intact. They have to be robust enough to survive the extreme vibrations, high G-forces, and other harsh conditions during launch.
“All those things have to be accounted for and they have to be tested for through our manufacturing processes,” Palcisco said.
The facility in Kirkland will include testing chambers that can simulate thermal shocks and run vibration, acoustics, and other tests. The ability to create those conditions on Earth is relatively unique in the space industry, Palcisco said.
“We actually pull all the air out of the chamber, create the vacuum-like environment of space, and then swing the temperatures from hot to cold to make sure the hardware can handle it and perform in those environments,” he said.
Scaling for space
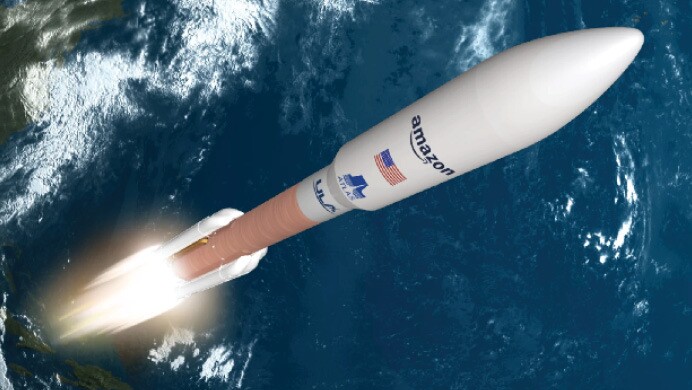
The team has to overcome many technological and design obstacles as they ramp up production. “At peak, we’ll be building up to four satellites per day to meet our ultimate goal of completing the Kuiper network,” Palcisco said, noting that some facilities can only build that many satellites in a year.
Palcisco and his team are overseeing the satellite components and material from the moment they arrive at the loading dock in Kirkland. He noted that the satellites have to be built according to “very strict rules and procedures,” so it’s imperative that the team is part of the process at every step.
Similar to factories manufacturing computer chips, the Kirkland facility must maintain high levels of cleanliness. Visitors will experience positive air pressures and high filtration, and see technicians wearing specialized clothing.
“We have to make sure there are no contaminants that will go with our hardware into space,” Palcisco said.
Solving that puzzle is harder because the team is building what is essentially an assembly line for satellites. Palcisco explained: “Historically, satellites are built at extremely low volumes in laboratory type conditions. The big challenge for us really is how do we adapt our processes so that we can hold the highest standards, and do them at scale, where we can make multiple satellites each day versus a couple of satellites per year.”
Ground control
That journey begins with the people working on Project Kuiper, which attracted professionals from diverse backgrounds. “We've certainly got folks who have a lot of space experience, but we've also got folks who come from industries like aerospace and automotive, where mass production is really a core competency,” Palcisco said. “They can help us apply automation in ways that drive variation out of process and make sure that every time you make a satellite, it'll come out the same.”
As Palcisco noted, the team is using automation and robotics to standardize their process. Some members of the team recently visited Amazon’s robotics research center in Boston, Massachusetts, where the company is developing robots for its fulfillment centers.
“We want to better understand where automation makes sense for us,” Palcisco said. “That collaboration has enabled us to be smart about where we apply it, and we have designed and built some of our own robots to do things that need to be done in very precise manners, like apply adhesives and measure antennas.”
The Kuiper team also uses connected torque tools to ensure that fasteners on the satellite are tightened to the exact same value every time. “Those tools will actually count how many fasteners have been torqued and store that information so that we can analyze it in the future to optimize our processes,” he said.
Internet for everyone
So how different is building jet engines from making satellites?
“Aerospace in general is a very well understood industry that's been developed over many years,” Palcisco said. “We are creating processes that haven't been done before, we iterate on those processes, and we decide what's the best for the satellite as that vehicle gets built and launched into space.”
“Our satellite constellation will bring internet connectivity to underserved populations around the world,” he added. “To be able to come to work every day knowing that you're having that kind of an impact—and at the same time building new technology—is really exciting. I think that's what gets people out of bed and brings them to work every day.”