I got into engineering because I liked to build things. Now, I’m an engineer who breaks things. I’m a senior hardware reliability engineer at Amazon Lab126, the company’s product innovation hub in Sunnyvale, California. My team designs and executes tests to identify ways to improve prototypes for new products. I’ve worked in the lab for nearly 10 years, and I’ve helped test and build many of Amazon’s popular products like Echo devices, Fire TVs, the Astro household robot, and of course, book lovers’ most beloved device—Kindle.
As a Kindle owner myself, I know how easy it can be to drop your device or spill on it from time to time—even when you’re a reliability engineer who’s particularly careful. That’s why I love being a part of the team that helps make these devices more durable, safe, sustainable, and cost-effective for our customers.
Our work requires a lot of strategic destruction, all in the name of building better products. We run dozens of different tests on prototypes for new Kindle models to deliver a reliable device that enables customers to read their favorite books. Here’s an exclusive peek at what some of that testing looks like.
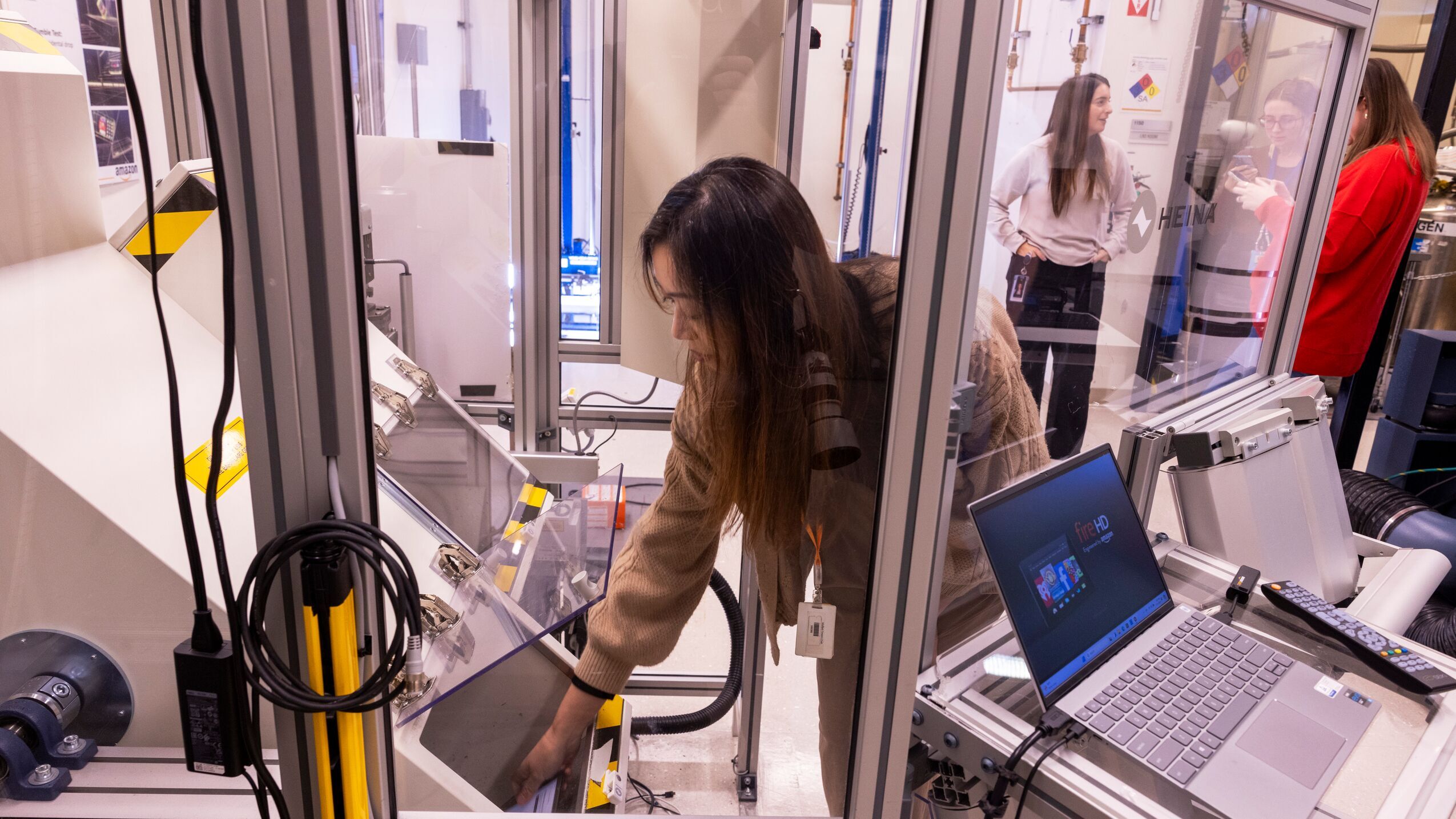
Our process begins by understanding how customers could potentially use their devices. We conduct user surveys and studies and use data from products already in the field to determine the typical and extreme user behaviors. We then collaborate with our design teams to develop products that satisfy use cases.
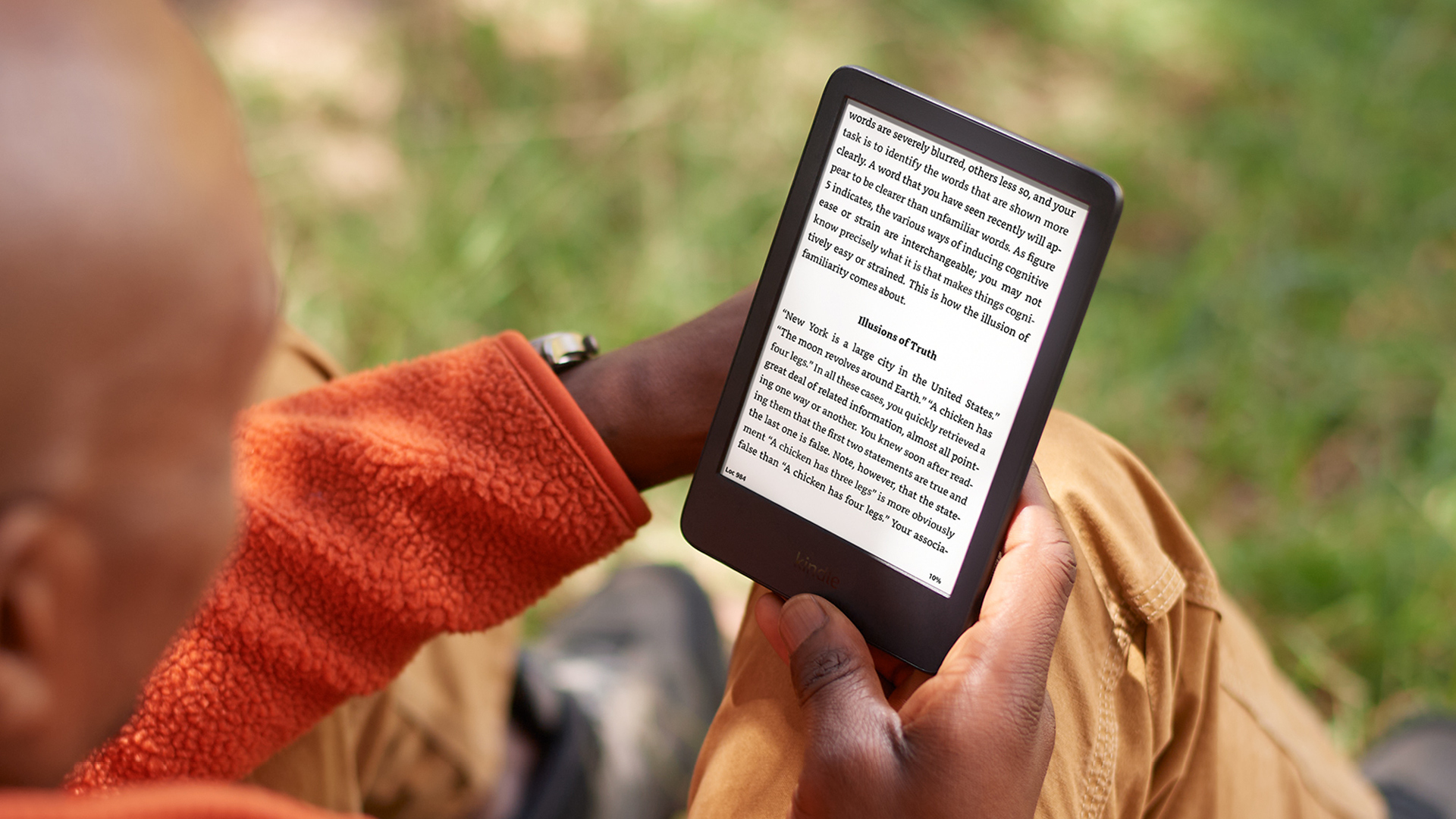
We test different materials to ensure each device is made from quality components. One of the coolest tests in our lab is the four-point bend test, which applies uniform bending pressure to the glass on devices to find out how much force the glass can withstand. This helps us determine which type of glass is best for a given device, identify any opportunities to improve design and manufacturing, and inform the criteria for future tests once we have the prototype.
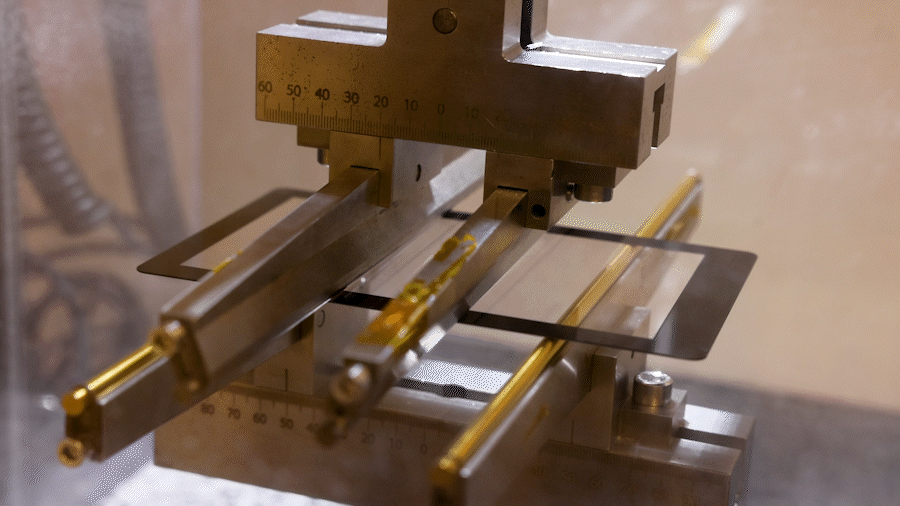
Once the product engineers create the initial design, we begin running simulated virtual tests to gauge product performance before they begin manufacturing the prototypes. We can simulate different scenarios like drops and other types of impact using a digital rendering of the device.
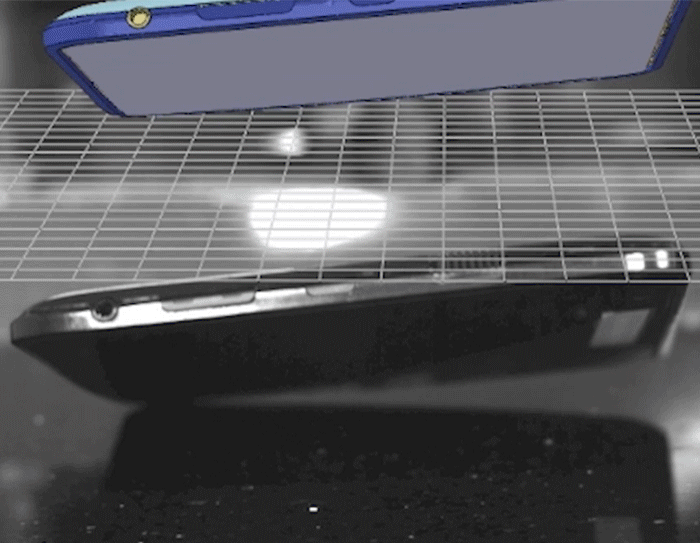
The fun really gets started once we have the prototypes. Our lab is full of various test stations that push Kindle devices to their limits. One of the most important tests is the drop test, where we drop the device multiple times, hitting different angles like the face, corners, and edges. This helps us find out how the device will withstand falls, taking into consideration that customers will drop it from different heights and on different surfaces.
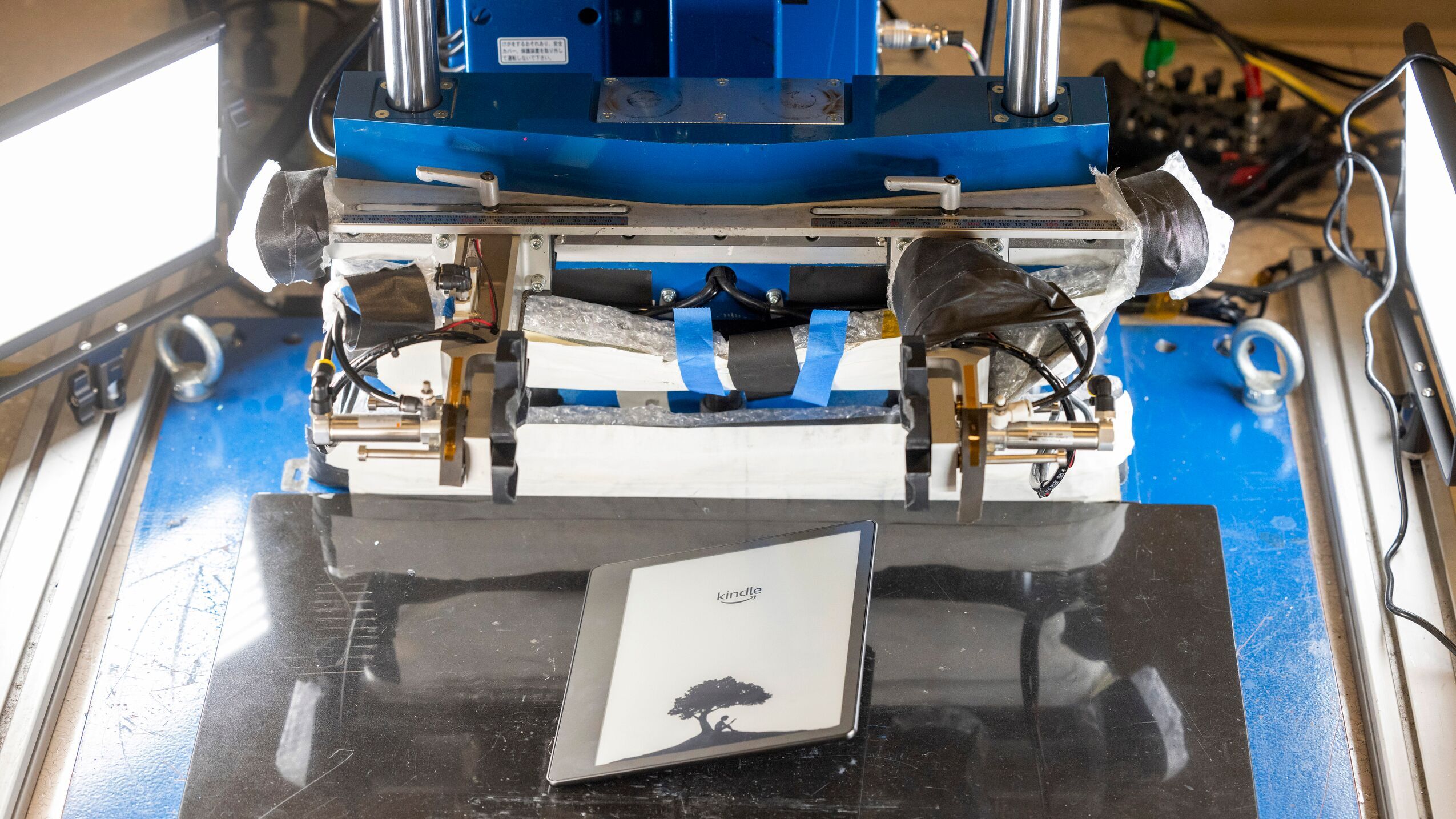
We also use the tumble test to simulate customers dropping the device. This test moves the e-reader around in a large, dryer-like machine to test its durability when dropped from random angles. We use a combination of this test and the drop test to gather information on both random drops and exact drop angles.
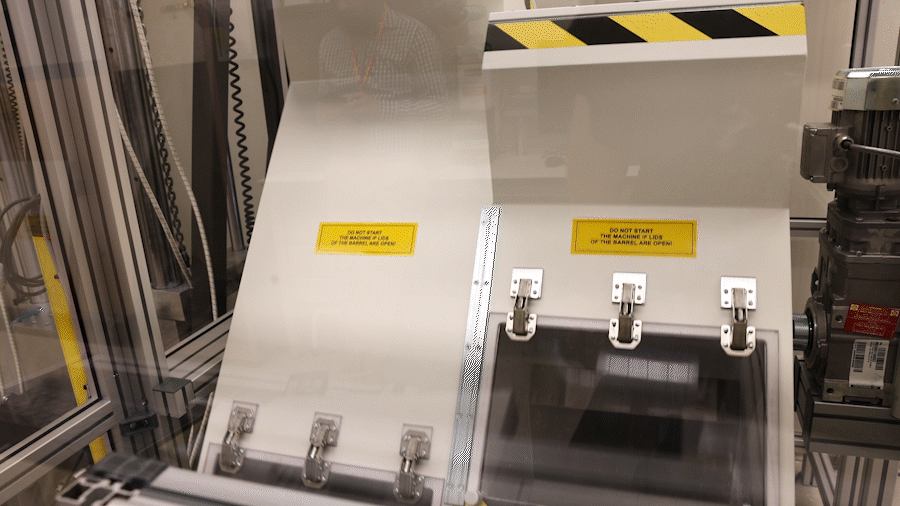
The backpack test simulates a customer carrying their e-reader in a backpack or bag. For example, a student may expose their Kindle to movement and pressure while carrying it in their backpack along with books and other heavy items. We run this test to assess and improve durability against that kind of mechanical pressure and vibration.
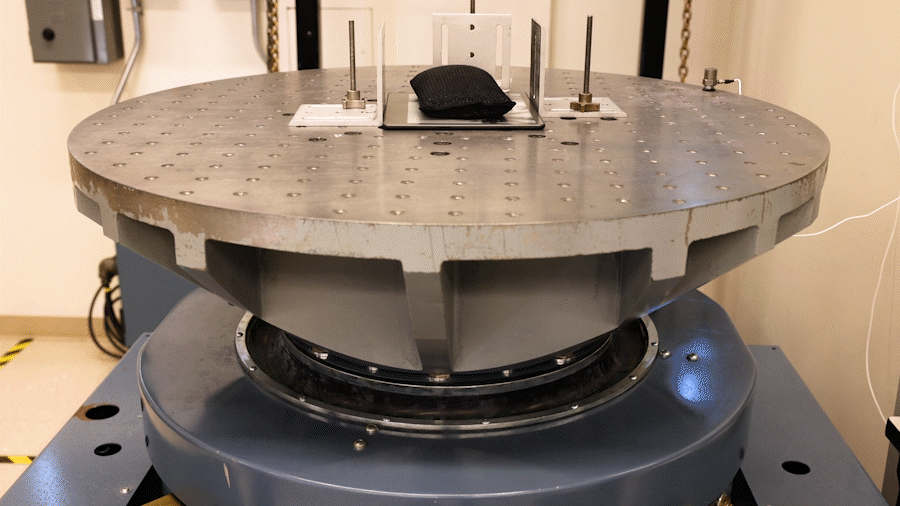
Kindle e-readers have a touchscreen display, so we use the touch test to mimic a customer’s touch. We estimate how many times our heavy usage customers may touch their device over its lifetime, then conduct user studies to understand what level of force they’ll likely apply each time. From there, we program the test to simulate that behavior and inform the design to perform over time.
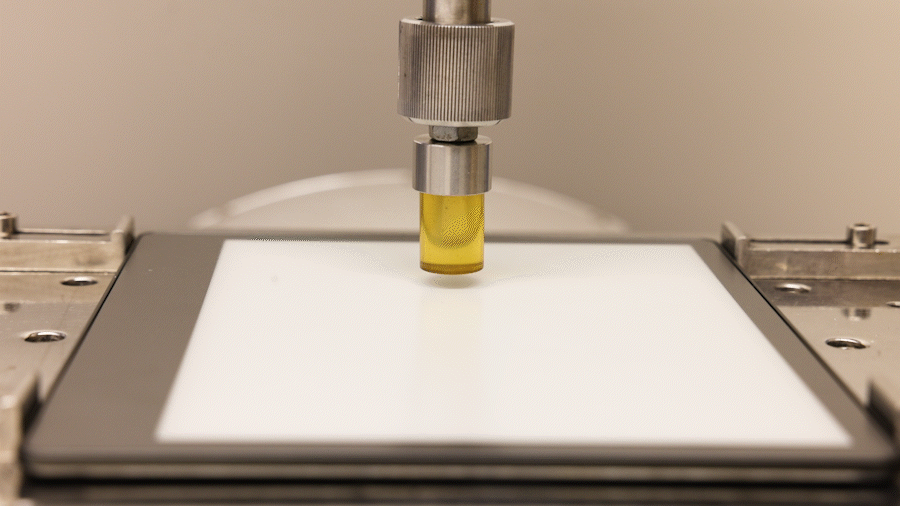
Devices are sometimes bent or twisted—like when customers place them at the bottom of a bag—so our process includes the twist and torsion cycle testing. We go back to our user testing to estimate how often and how much customers will twist and bend a Kindle, then design a test to approximate how a prototype will withstand twisting and torsion over time.
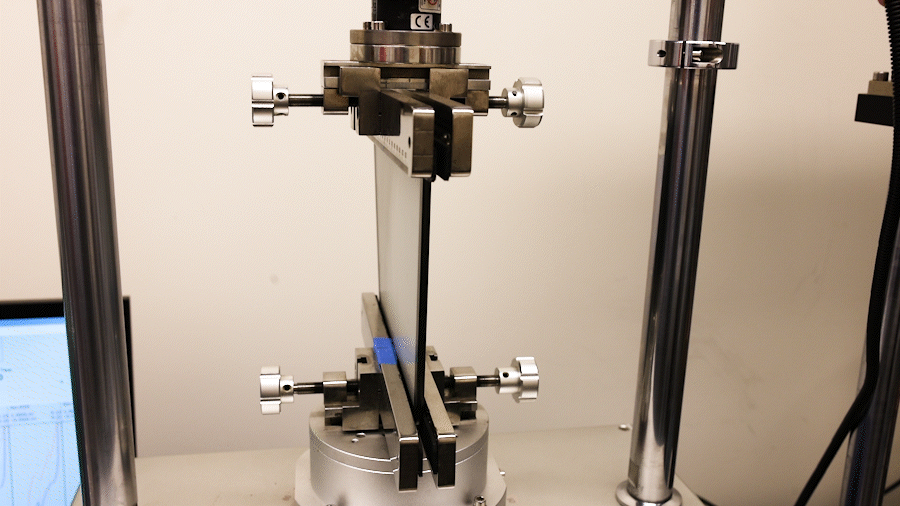
Many external surface materials used in electronic devices can be sensitive to household chemicals like sunscreens and lotions. That’s why chemical testing is another important part of our testing process. We test a range of products like food condiments, lotions, and oils to try to build devices that are less likely to degrade when exposed to common products. We even test with sunscreen, so don’t forget your SPF when you’re reading outside!
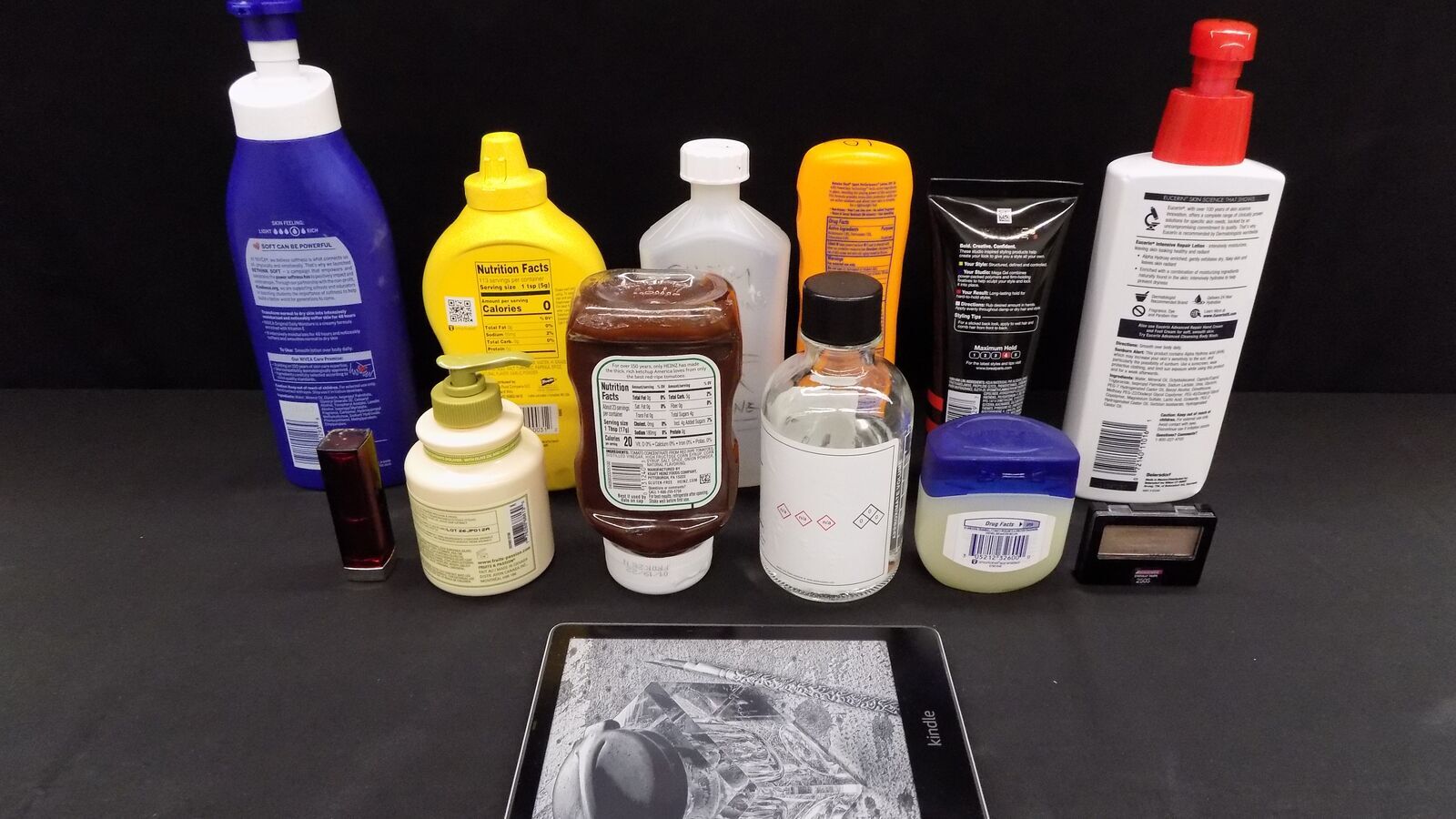
We also test each new device to check whether the materials are able to withstand a certain amount of sun exposure. Our solar exposure test applies ultraviolet (UV) light to observe how devices react. For a Kindle, we want to see if the materials crack, if the colors fade, or if the display degrades when exposed to sunlight for aprolonged periodof time. The photo below shows how the solar exposure test works using fabric for Kindle cover.
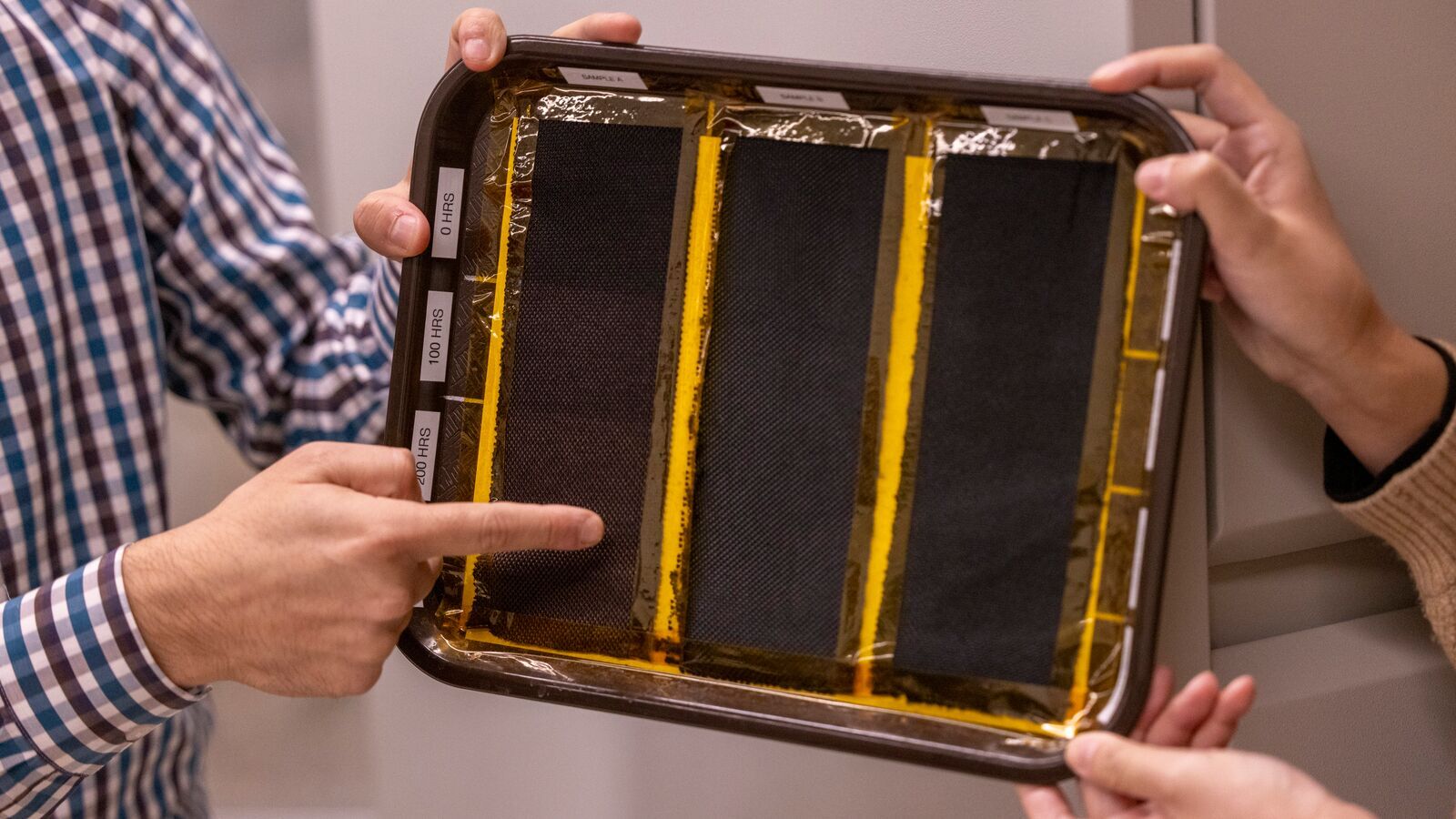
Some of our Kindle devices are waterproof, so we test to confirm the devices can withstand accidental water immersion before they end up in customers’ hands. Fun fact: We also test Kindle devices in bubble bath in case you use your device for relaxing baths.
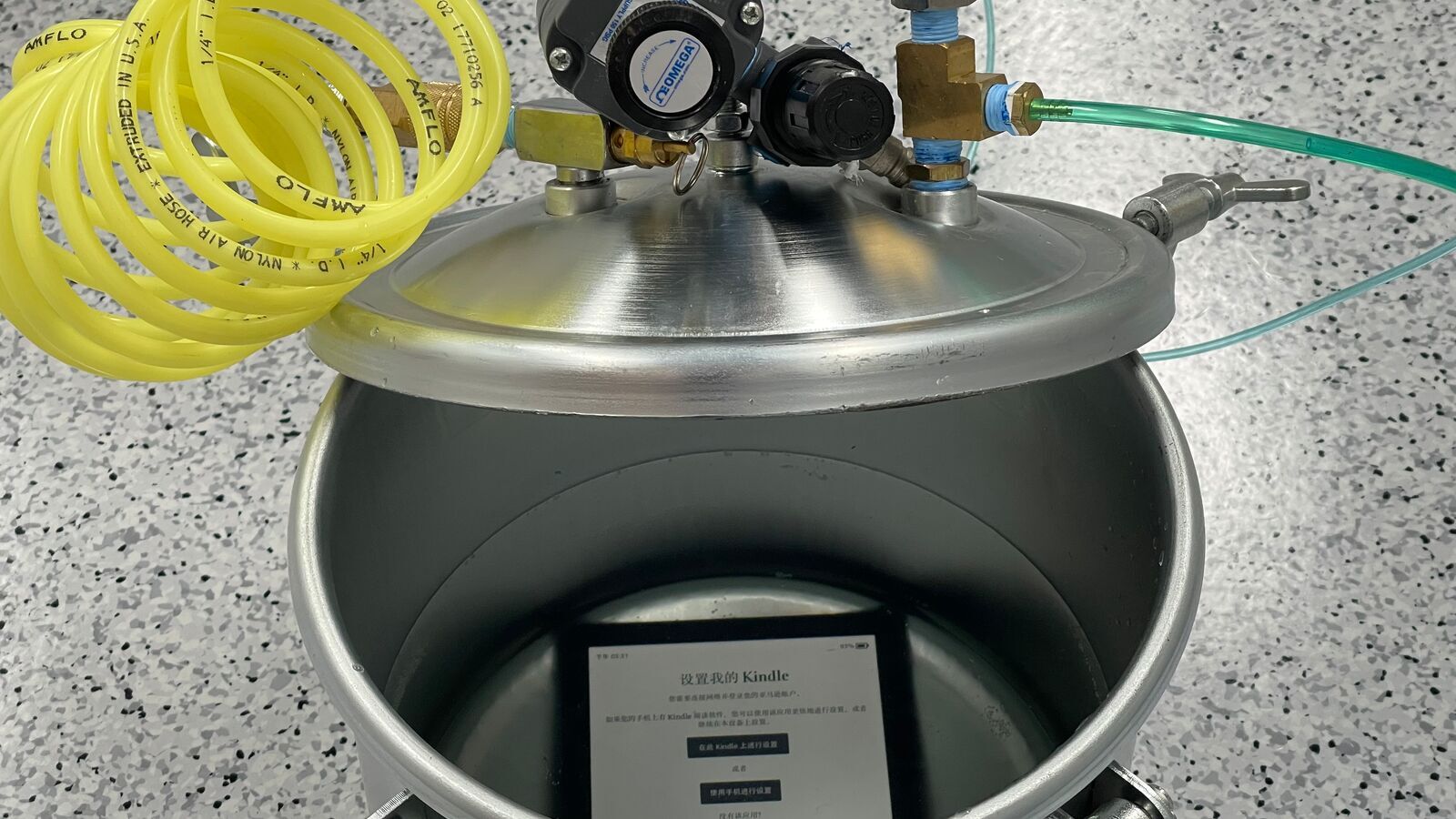
Because the Kindle is a mobile device, we try to develop testing that will help the product perform in a lot of different on-the-go scenarios. These are just some of the many simulated and physical tests my team runs on new Kindle prototypes.
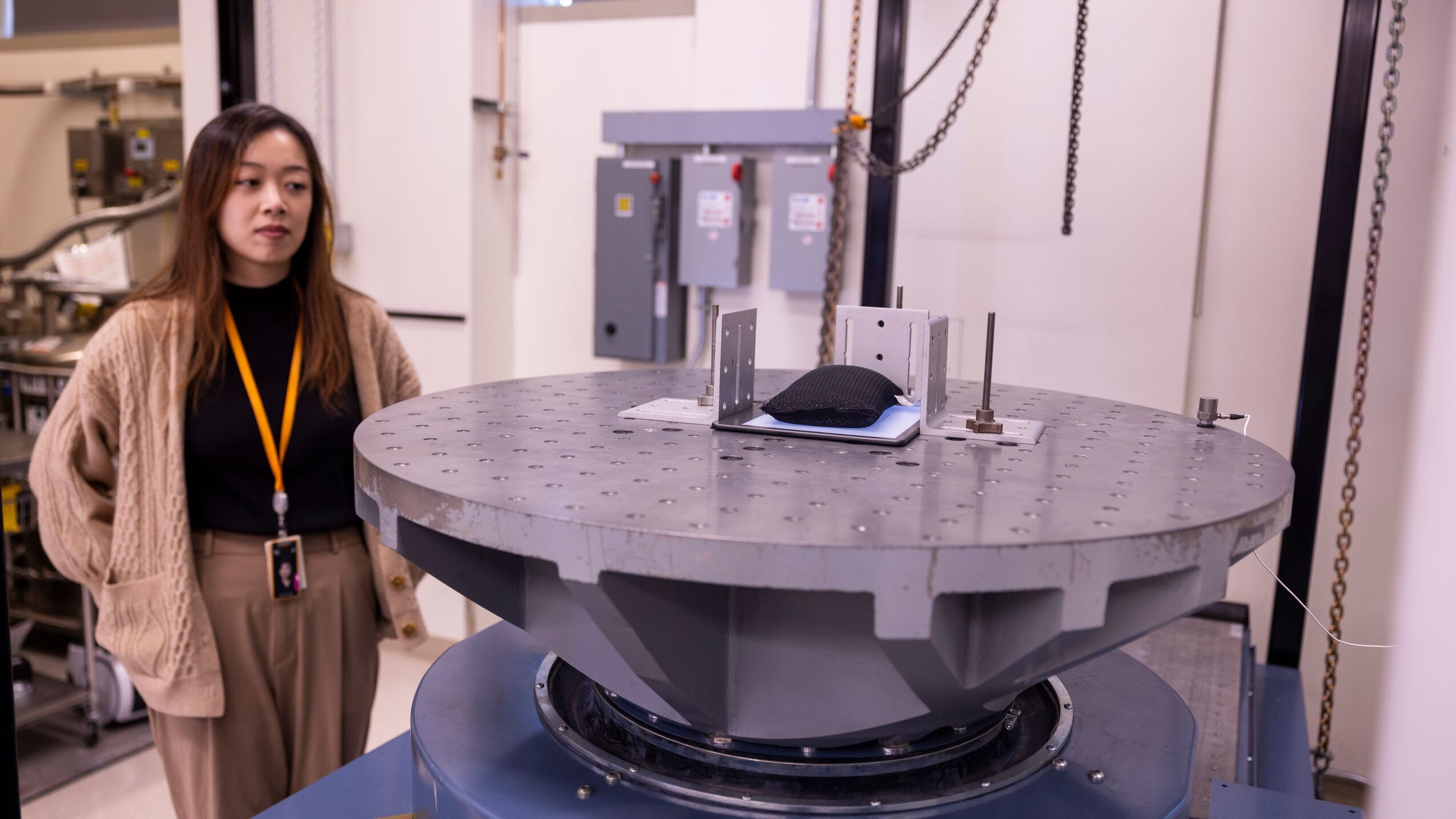
My favorite part of my job is having the ability to impact critical design decisions that help bring better devices to our customers. As a Kindle fan myself, I’m glad I can play a role in helping fellow readers take their favorite books with them on the go.
Trending news and stories
- Meet Project Rainier, Amazon’s one-of-a-kind machine ushering in the next generation of AI
- Amazon launches a new AI foundation model to power its robotic fleet and deploys its 1 millionth robot
- Project Kuiper and U.S. National Science Foundation sign satellite coordination agreement
- Amazon MGM Studios sets Denis Villeneuve as director of next James Bond film