One of the things that keeps me excited to come to work at Amazon every day is the ability to build new technologies that have a positive impact on our employees and customers around the globe. A big part of that is robotics—and specifically, how it continues to improve safety for our teams. In fact, the safety improvements we’re making with our robotics makes me more excited about the future than ever.
We know that improving safety in a company of Amazon’s size and complexity requires long-term investment and commitment. This year alone, we are investing more than $550 million into safety-related projects and initiatives, and we have more than 8,000 safety and health professionals whose sole responsibility is to protect our people and partners. As a result, injury rates across our network have declined. We are helping to build on that progress by continuously collaborating with our safety and operations team.
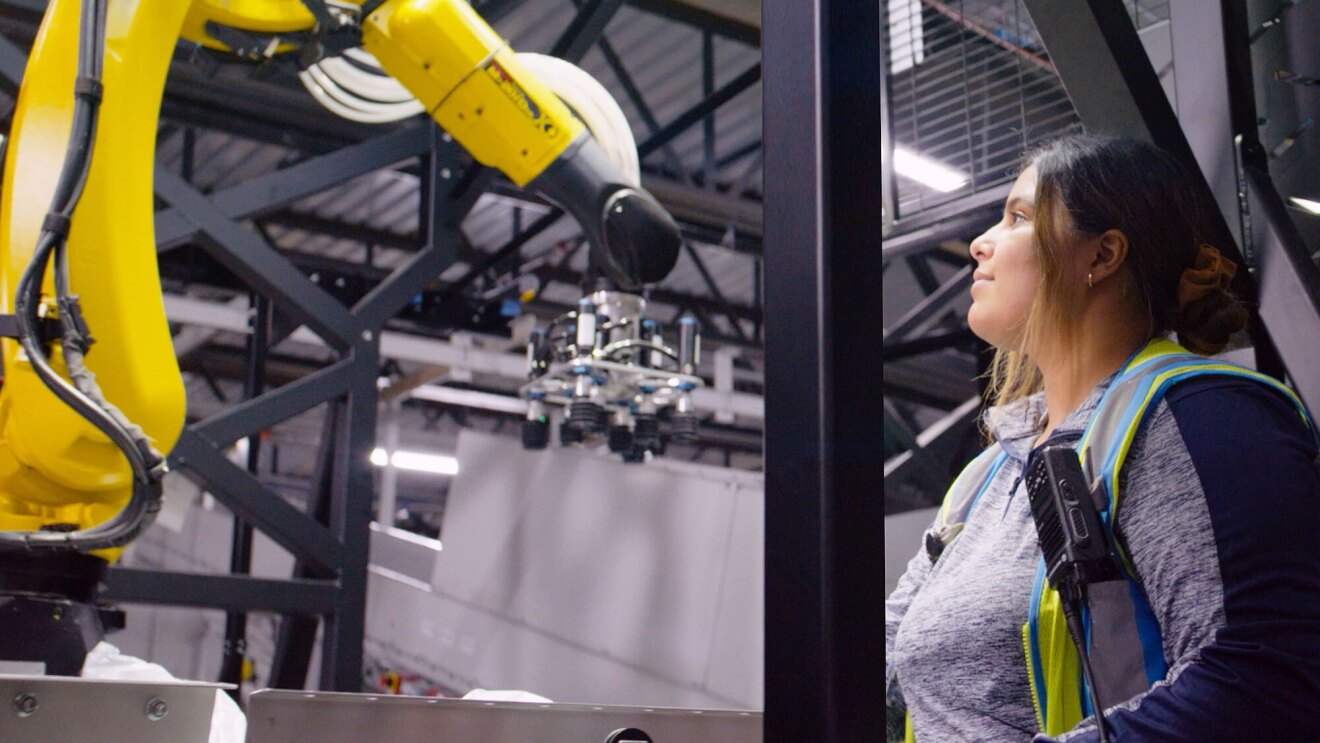
Ten years ago, when we first rolled out mobile robots in our facilities, we were confident that they would improve workplace safety. And, we were right. Robotics technology working alongside people alleviates our employees’ physical workload, like reducing their walking distances or their repetitive bending and twisting to pick up packages. Anecdotes from our team, like this one from Robert Morua who works at a fulfillment center in Texas, inspire me and demonstrate that we’re on the right track:"I started off in a very active entry-level position picking and packing product, and the introduction of robotics at our fulfillment centers has positively changed the employee experience because it’s helping reduce those repetitive tasks. As a leader today, I see the safety impact it has at scale for thousands of employees at my site and other robotic facilities across the network.”
As the number of mobile robots has grown from thousands to more than 750,000, we want to ensure robotics are supplementing employee’s work and creating a safer environment. And, from what we see, that’s happening. Company data shows that, in 2022, recordable incident rates and lost-time incident rates were lower at Amazon Robotics sites than non-robotics sites.
Here are two improvements based on our robotics that I’m particularly excited about.
Workstation safety
Amazon operations employees pick and pack billions of products every year at workstations that use artificial intelligence (AI), computer vision, and machine learning to help simplify tasks and keep our employees safe. To reduce the risk of repetitive motion injuries, we introduced new AI models to better plan and distribute where inventory goes and to help ensure our employees pack items in an ergonomically friendly way. These changes automatically shift work to the employee’s “power zone” (the part of the body between midthigh and midchest), which reduces the frequency that employees have to reach or bend to store products, and helps them lift and carry items with the least amount of effort.
Sequoia, our latest robotics solution for inventory management, introduces a newly-designed ergonomic workstation, where containers are delivered to an employee in a manner where they can do even more of their work in their power zone. This system helps minimize how often employees will have to reach above their heads or squat down to pick customer orders, further supporting our efforts to lower the risk of injuries.
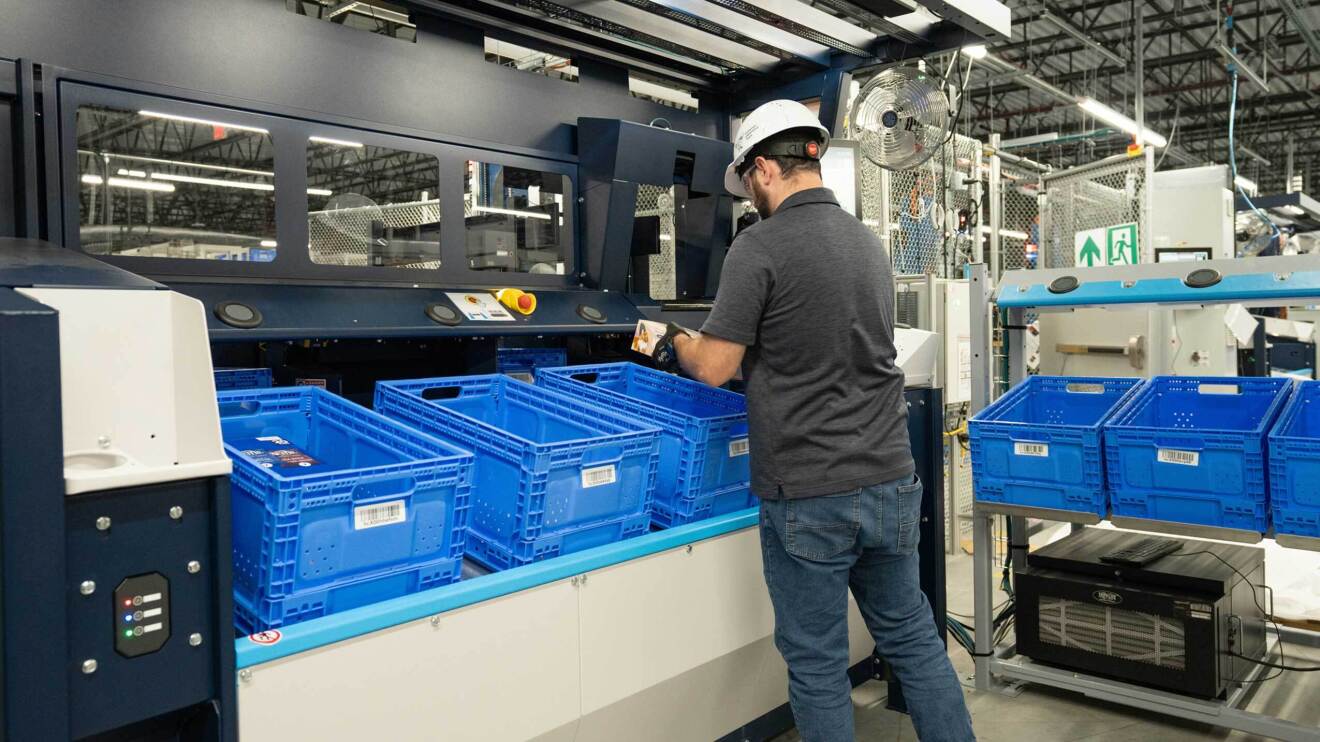
Employee feedback has helped us continuously make improvements to our software and hardware to reduce risk globally. As Melissa Hibbard, who leads global robotics safety engineering, said in one of our recent conversations, “Our goal is to build technology for employees to work smarter and not harder. Using employee feedback and other insights, we test software and hardware updates on our systems to assess their safety impact and broadly deploy those that contribute to our overall safety program.”
Repetitive motion reduction
Last year, we signed the MSD Pledge, created by the National Safety Council, which includes a commitment to reduce musculoskeletal injuries by 2025. Working toward this commitment is a companywide effort that requires a comprehensive safety strategy that we apply at all facilities, whether or not they have robotics.
Our newest industrial robotics focus heavily on human-robotics collaboration and human-centered design. Systems like Robin, which uses a robotic arm to help sort customer orders, are helping reduce repetitive employee movements like lifting, stacking, and turning at our facilities. With more than 1,000 Robins deployed across our network, this technology has now assisted with sorting more than 2 billion packages.
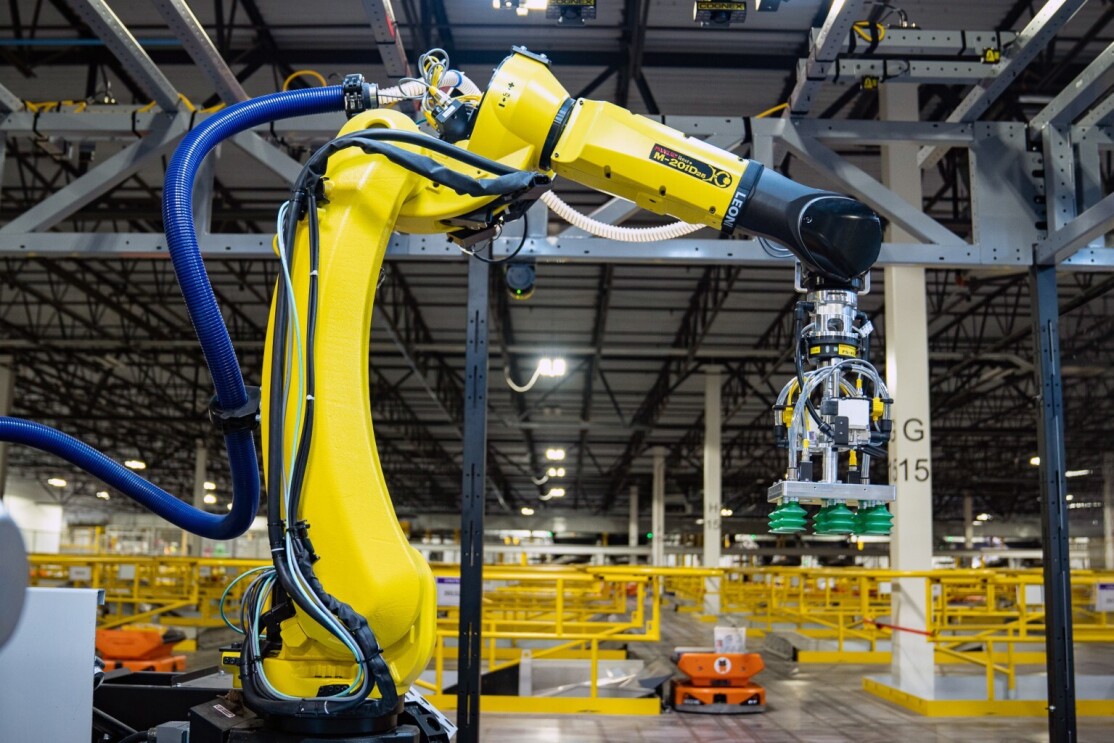
From the research and development we’re undertaking to build these latest collaborative robotic systems to the updates we’re making to existing technology, we’re making progress on operational safety and creating new career paths in the field of robotics where employees have the opportunity to develop new skills and grow professionally. Our innovation has led to the creation of more than 700 categories of new jobs at Amazon, including positions like flow control specialists, robotic floor monitors, and reliability maintenance engineers.
As employees gain new skills and move into roles working alongside our latest technology, their insights on how our robots help simplify their work and make our operations safer is essential. Together, we’re just getting started on the many innovative ways we can use technology to improve our workplace, and I’m more excited than ever for the journey ahead.
Trending news and stories